Do-it-yourself installation of concrete floors, the main varieties, stages and pouring technology. Concrete flooring is the most common subfloor for flooring. They are made not only in houses and apartments, but also in other buildings related to the non-residential fund. The strength of the structure depends on the observance of all stages and technologies of work.
The main types of concrete floors
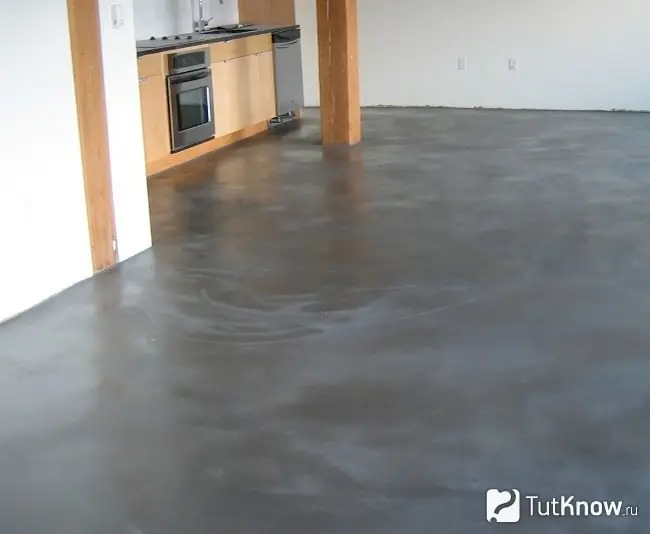
Before answering the question of how to make a concrete floor, you should find out what types of them exist and what is their difference. There are three main types of concrete floors:
- Single-layer cement-sand floor screed … It is used for rooms with a small area. Due to the lack of additional layers providing rigidity, such a structure is not resistant to heavy loads. It is most reasonable to pour a single layer concrete floor in a small house, apartment, outbuilding or garage.
- Multi-layer floors … They have a more complex structure. In the manufacture of structures of this type, concrete is poured in several layers. Most often, multi-layer concrete floor technology is used for the reconstruction of floors.
- Reinforced floors … This is the most durable type of concrete floor. Due to the use of reinforcement in their construction, the thickness and weight of the entire structure can be significantly reduced. In this case, the strength of the floors will be higher. For reinforcement, rods, mesh and fibers made of steel, as well as synthetic materials are used. Installation of reinforced floors is carried out in those rooms where there is a high load on the floors: in factory shops, hangars, car parks and other large buildings.
Features of the device of the concrete floor
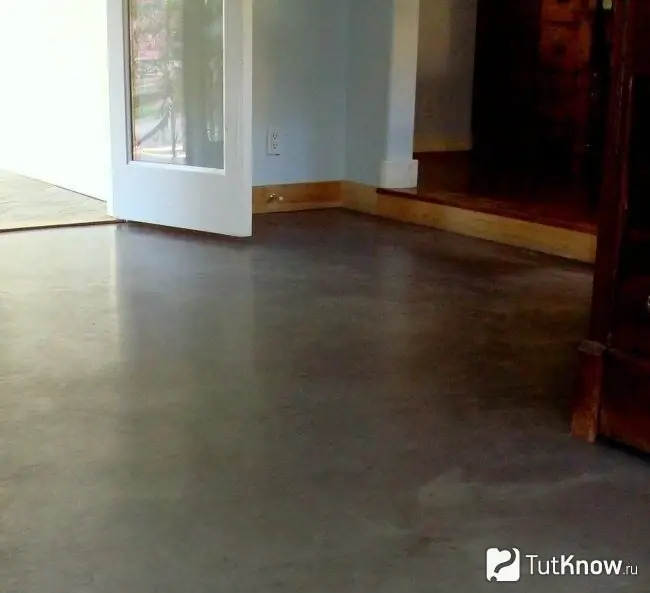
The technologies for installing concrete floors may differ depending on the purpose of the building and the specifics of the room. In addition, the purpose of the work is of great importance. This can be leveling the surface, warming the floor, changing the height of the base, etc. By applying various methods, it is possible to ensure high strength and durability of the structure. Concrete flooring can be done over any surface. This can be a subgrade, old concrete pavement, or even wood flooring.
In order to make a high quality concrete floor, it is necessary to use high-quality materials, strictly follow the technology, and also comply with all building codes and regulations (SNiP). They depend on the characteristics of the building and its purpose.
Before starting work on the installation of floors, it is necessary to select concrete. The mass of the structure, as well as its strength, will depend on its density and composition. The higher the load on the floor, the heavier type of material should be used. Depending on the active substance, the material can be cement, silicate or polymer concrete. By the diameter of the grains of the aggregate, coarse and fine-grained compositions are distinguished, they may include crushed stone, pumice or expanded clay. To speed up the workflow when installing floors in buildings with a large area, special equipment should be used. This will automate all processes. To pour a concrete floor in a garage, apartment or other small room, it is enough to use a conventional concrete mixer.
Concrete floor installation technology
The construction of concrete floors is divided into several main stages: preparation of the base, installation of insulation, reinforcement, placement of beacons, installation of guides, preparation of mortar and its laying, surface treatment, laying of expansion and expansion joints. Some changes can be made to the technology of the work. This may depend on the tasks set and the expected result. However, the sequence of actions must not be interrupted.
Substrate preparation for concrete floor
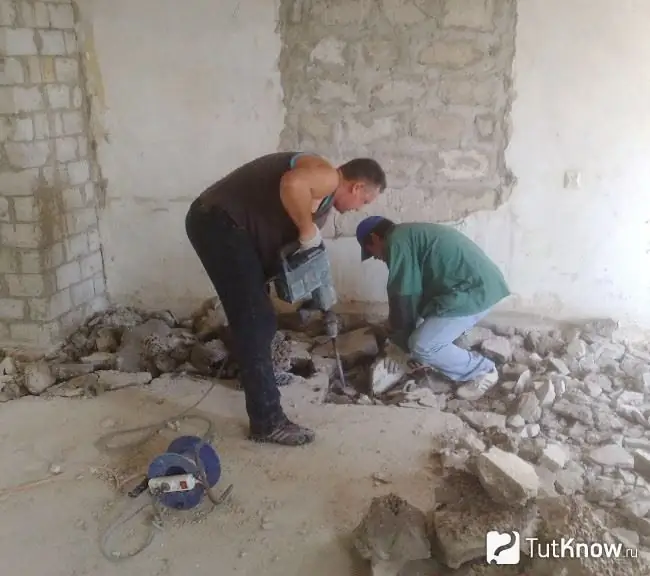
Before starting the installation of concrete floors, it is necessary to carry out a number of preparatory work. Different substrate surfaces require different technologies.
If work is carried out with an old concrete pavement of poor quality, it is necessary to remove all their layers up to the overlap. A puncher is suitable for these manipulations. After that, all debris and dirt must be removed from the work surface. If the concrete floor screed is in good condition (there are no serious damages and cracks), you can not waste time dismantling it, but immediately proceed to the next stage of floor installation. If small defects in the coating are still present, it is necessary to widen all the faults and fill them with a solution of sand and cement or any other repair mixture. After that, the surface must be leveled and cleaned of dirt and debris.
When carrying out work on the construction of a concrete floor on the ground, it is necessary to perform the following steps:
- From the bottom point of the base of the doorway, measure one meter in height and put a mark. Further, at the same level, using a level, you need to mark each wall around the perimeter of the room. From each mark down, it is necessary to measure a distance equal to one meter. The resulting level will be the upper boundary for pouring concrete. It will be easier to navigate on it if you drive nails into the marked points in the corners of the room and stretch a thick thread or twine between them.
- Next, you need to remove a layer of soil 25 centimeters, and tamp the surface of the pit so that it is even and dense. With a well-done work, after pressing on the soil, there should be no traces. This will prevent the floor from sinking and cracking.
- The working surface is covered with river sand, moistened and tamped tightly. The layer height should be 10 centimeters. A layer of sand is covered with gravel or expanded clay, also spilling them with water. The thickness of such a pillow should be 5-10 centimeters.
- The next layer should consist of sand, which is tamped in the same way. If the project provides for laying communications under a concrete screed, it is best to lay them at this stage. In this case, you should use special protective covers or boxes.
- The surface is tamped, leveled and covered with the last layer of crushed stone, 10 centimeters thick.
- In conclusion, everyone is covered with sand.
Note! The size of crushed stone should be 4, 5-5 cm. And the thickness of the concrete screed cannot be less than 2 cm. In order to maintain the thickness of all layers, you can apply appropriate marks on the walls before starting work.
Waterproofing device when pouring a concrete floor
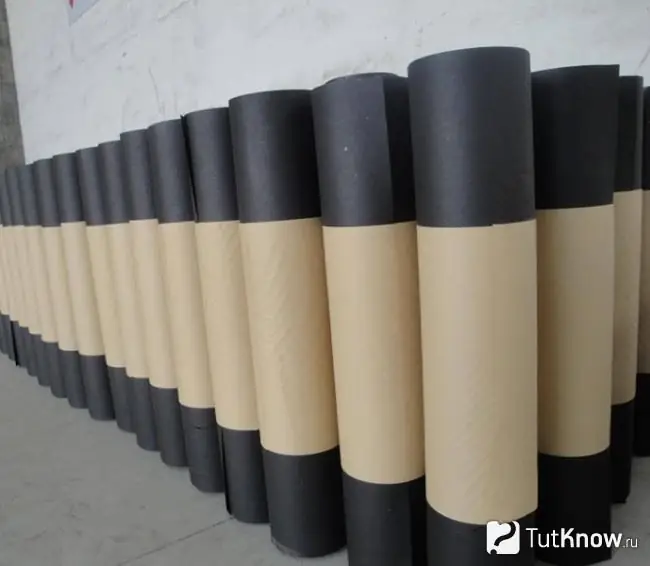
Concrete floors need quality protection against moisture circulation. Violation of the installation technology at this stage can cause a high level of humidity in the room. This will affect not only its internal microclimate, but also finishing materials, pieces of furniture and appliances. There are no strict requirements for the waterproofing material. The choice of coverage depends solely on the financial capabilities and preferences of the owner of the premises. It can be a modern roll material, several layers of roofing material or an ordinary polyethylene film (while its density should be more than 200 microns).
The insulating material should only be installed after it is clear that the rubble layer will not damage it. To do this, you need to make sure that the crushed stone is tightly compacted and does not have sharp corners. If it is not possible to lay the waterproofing directly on the pillow, it is necessary to fill it with a thin layer (about 4 cm) of liquid concrete. After that, you need to wait for it to harden and only then lay the insulating layer.
The material is distributed over the entire working surface with an overlap of at least 20 cm. Its edges must reach the upper boundary of the concrete pour and be firmly attached to the walls and fixed to each other.
The laying of concrete floors can be accompanied by the installation of thermal insulation material. It can be expanded polystyrene, polystyrene foam, mineral wool, expanded clay, polyurethane foam, etc. The choice of insulation depends on the characteristics of the building, its purpose and construction estimates.
Concrete floor reinforcement rules
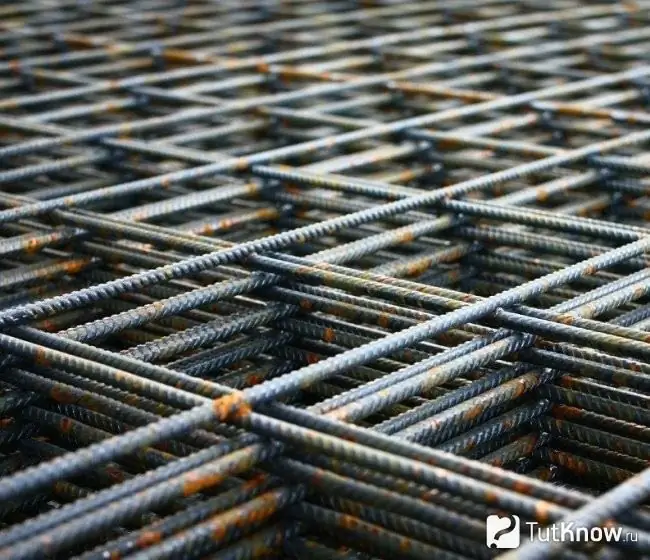
A concrete floor screed needs to be reinforced if it is expected to be subjected to heavy loads. Reinforcement allows you to strengthen the floor and evenly distribute the load. Regardless of the material of the frame, its installation is carried out at a distance of 2-3 cm above the surface of the base of the floor. To do this, use special fasteners ("chairs").
As a material for reinforcement, meshes made of metal or plastic are used. They can be made with your own hands by welding from a thin wire (3-5 mm thick) or you can buy ready-made products. Also for this purpose, you can make a frame from reinforcement. Its thickness can vary from 8 to 18 mm.
Advice! The mesh size of the reinforcing mesh should be 10 by 10 cm. If the load on the concrete floors is not too large, you can increase the cells to a size of 15 by 15 cm.
Production of formwork for pouring a concrete floor
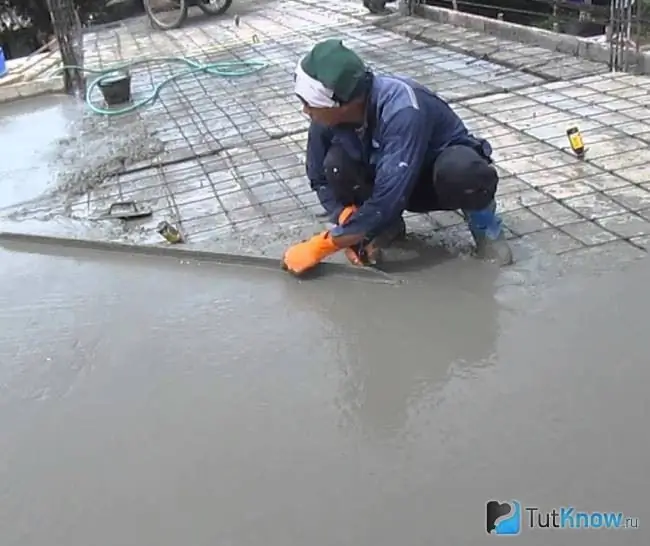
The construction of concrete floors in large and medium-sized rooms can be facilitated by the construction of formwork. For this, the working surface is divided into equal rectangular sections. In this case, it is desirable that their size allows the mortar to be filled in a maximum of 1-2 passes.
Further, the technology of work consists of the following steps:
- The guides are laid on a previously prepared base using cement mortar. Between them, it is necessary to install the formwork, forming a rectangular container for laying concrete. The height of the structure must correspond to the maximum concrete pouring level. Guides can be made of wooden boards, moisture-resistant plywood, metal pipes.
- All structural details must be treated with a special formwork compound. Thanks to this processing, it will not be difficult to separate all the elements from the hardened concrete.
- After the cement mortar connecting the guides hardens, you can start laying the concrete mortar.
- Dismantling of the formwork is carried out only after the concrete has completely hardened. The voids formed after the removal of the structure are filled with a new solution.
Note! When installing the guides, it is necessary to strictly monitor compliance with the level of the upper boundary of concrete pouring using a level. The slope of the finished floor will depend on this.
Concrete floor pouring process
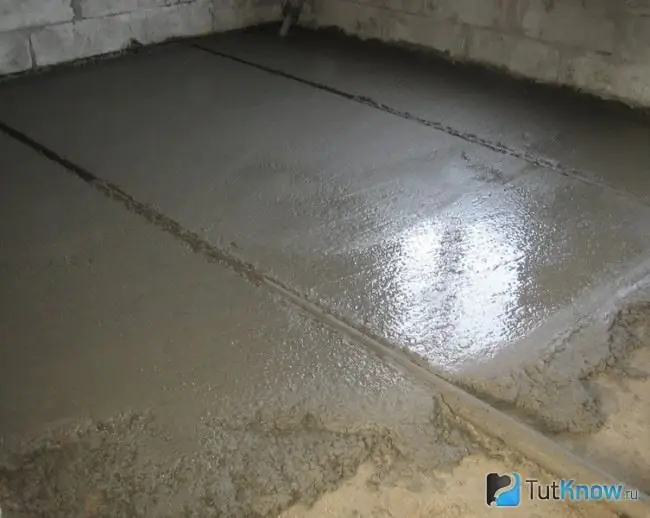
Concrete floor technology assumes that the process of pouring the solution will be carried out in one go. For this reason, when working with large areas, it is desirable to be able to order a sufficient amount of concrete mix directly from the factory.
If financial opportunities are limited, you can get by with the means at hand and prepare the solution yourself. To do this, you need to prepare a concrete mixer, cement grade not lower than M-300, clean sand without impurities and crushed stone.
The technology for preparing the solution is simple: for 1 part of cement, you need to take 2 parts of sand, 4 parts of crushed stone and dilute with 0.5 parts of water. The mixture should be thoroughly kneaded in a concrete mixer until a plastic consistency is formed and evenly laid in the formwork. To do this, using a shovel, the solution is carefully leveled over the entire area of the structure, making piercing movements in the vertical plane.
In order to eliminate excess air from the concrete mixture and give it a denser structure, a special vibrating device should be used. They need to work until cement milk is formed on the surface of the solution (a liquid mixture of water and cement without other impurities).
After carrying out work on vibration compaction of the mixture, it must be leveled with a rule. The device is placed on the guides and gently attracted to itself, making smooth undulating movements from side to side. It takes about five weeks for a concrete floor to build up a margin of safety. Moreover, its surface should be regularly moistened.
The durability of the structure and its appearance depends on the surface layer of the concrete floor. It must be liquid and chemical resistant, shockproof and hygienic. For this, the finished structure is coated with special compounds - impregnations, primers, varnishes and paints.
Advice! The laying of the concrete solution is carried out starting from the far wall of the room towards the exit. How to make a concrete floor - watch the video:
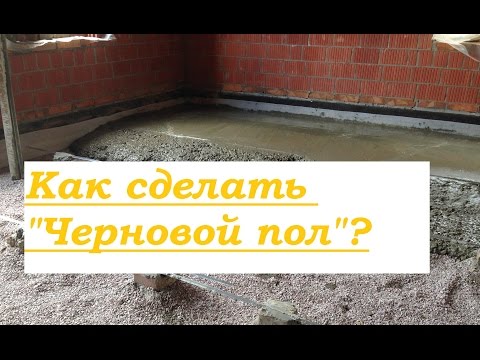
Installing a concrete floor with your own hands is a difficult, but quite doable task. At the same time, it is very important to observe all the subtleties of the technological process. A responsible approach to this issue will allow you to get a high-quality structure that will withstand heavy loads and adequately fulfill all its functions.