The main specificity of the expanded clay insulation works, its strengths and weaknesses, floor preparation and insulation technology, the creation of a concrete screed and final surface finishing. Thermal insulation of the floor with expanded clay is one of the most well-known methods of its thermal insulation. Many synthetic heat insulators, which were in demand earlier, are being replaced by natural heat insulators, which are safer for humans and pets. Considering the relatively low cost of material and consumables, it is not surprising that it has earned such popularity.
Features of thermal insulation of the floor with expanded clay
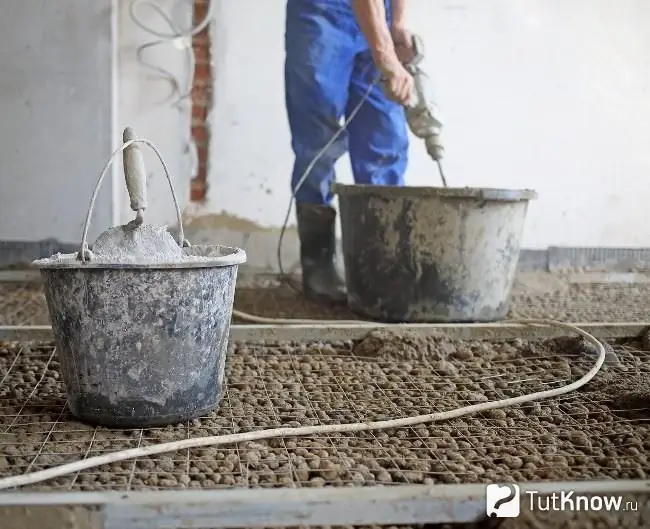
Expanded clay refers to natural insulation, since it is made from clay and shale-containing rocks, which include no more than 30% quartz in its basis. During the manufacturing process, the raw materials are heat treated in special ovens. The temperature acts on it in such a way that it is sintered and forms granules of various sizes. During production, it is not possible to achieve the release of granules of the same size. Therefore, expanded clay is subdivided into the following fractions: sand - 5-10 mm, crushed stone - 10-20 mm, gravel - 20-40 mm. The material is lightweight and porous. Experts recommend it as a reliable and effective heat insulator, since it is not only harmless to the health of the inhabitants, but at the same time reduces the cost of insulation, as well as further maintenance of the building. Which expanded clay is better for floor insulation depends on the type of building and its purpose. To achieve the maximum effect of thermal insulation with this material, the features of the floor surface on the first floors of structures are taken into account.
During the calculations, it is necessarily taken into account that this layer of only 10 cm has an effect that is equal to 20 cm from wood insulation. To fill up expanded clay around the perimeter of the insulated floor or to mix with a concrete screed, each owner decides for himself.
If you are interested in how to insulate the floor with expanded clay, pay attention to its main properties in combination with other materials. One of the common methods of thermal insulation is mixing cement with expanded clay granules. As practice shows, it is this option that improves the insulation characteristics of indoor floors. On the other hand, the main advantage of this material is the presence of air bubbles in it, which are obtained during its production.
When we insulate the floor with expanded clay with our own hands, mixing granules with a cement-sand mortar, we achieve a deterioration in its thermal insulation qualities due to the presence of water in the composition. That is why professional construction crews in many cases prefer the dry method of insulation. But the use of wet solutions is in demand at those facilities where the floors are characterized by significant differences and it is required to level them with a new concrete screed. In addition, it is much easier to work with solutions than with dry expanded clay. It's important to know! Granular expanded clay must be laid so that it is reliably insulated from moisture that may enter from below. Even in cases where the heat insulator is not placed directly on the earthen base, one cannot do without covering it with a waterproofing film. The height should be such on both sides that it rises several centimeters above the insulation.
Advantages and disadvantages of floor insulation with expanded clay
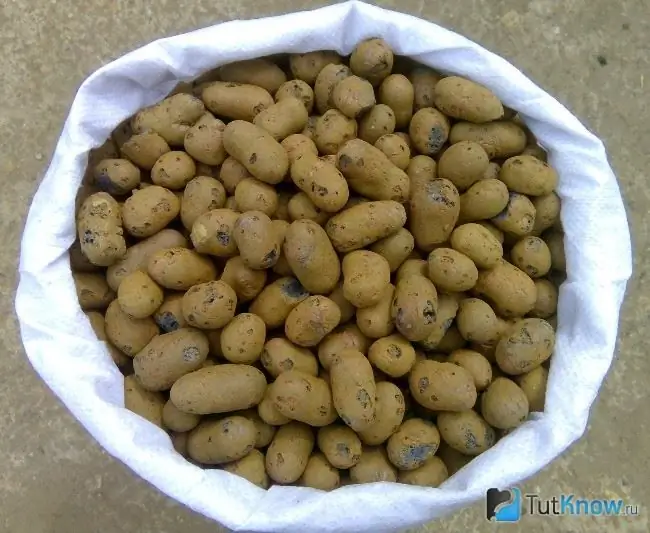
The main positive characteristics of this insulator are as follows:
- It is completely harmless to humans and pets, since no chemicals are used in its manufacture, but only exclusively natural materials.
- In addition to heat-insulating qualities, it acts as a good obstacle to the penetration of extraneous noise and sounds into the room.
- Expanded clay is characterized by increased fire resistance and resistance to significant temperature fluctuations.
- It perfectly withstands even the most severe frosts, preventing heat leakage from the building.
- Simple installation technology makes it possible not to involve outside specialists at the stage of such work.
- Expanded clay is practically not subject to physical, biological and chemical effects.
- You can achieve different values of thermal insulation by changing the size of the fractions of the material.
There are, of course, certain disadvantages that distinguish floor insulation with expanded clay. Firstly, it is rather high fragility, which it owes to natural raw materials. This can significantly complicate the creation of an insulating layer. Therefore, it is necessary to lay expanded clay with maximum care so as not to violate the structure of the granules - otherwise it will lead to a violation of the insulating qualities.
Secondly, it is worth mentioning the moisture-absorbing characteristics, which can also be a real drawback. This is due to the fact that the granules only absorb moisture, but do not give it out.
Another negative quality is the thickness of expanded clay. It automatically leads to the creation of a rather thick insulation layer. Consequently, such thermal insulation is not entirely suitable for rooms with low ceilings, because the volume of space will significantly decrease.
Technology of floor insulation with expanded clay
These works are not particularly difficult if you carefully follow the recommendations given here. This does not require construction qualifications, but you must adhere to the specified algorithm.
Preparatory work before installing expanded clay

Before proceeding with thermal insulation, it is necessary to carry out a number of works to prepare the floor surface. It may include removing old flooring, old logs, and fixing structures. All this can be left only if the wear of the elements allows them to be reused.
When it comes to insulation on a ground base, then it is first carefully leveled and then compacted. A layer of gravel or crushed stone with a height of about 30 cm is laid on it. A 10-cm layer of sand is poured on top of these materials.
For concrete substrates, it is sufficient to remove the protruding folds with a grinder with concrete attachments. Pits and grooves are sealed with leveling compounds or putty.
After that, the floor is cleaned of debris, particles and dust, wet cleaning is performed. Once the surface is completely dry, it is covered in 2 layers of primer. The base is ready for insulation.
For country and cottage-type houses, it is best to make a choice in favor of insulation along the logs.
Instructions for installing expanded clay on the floor
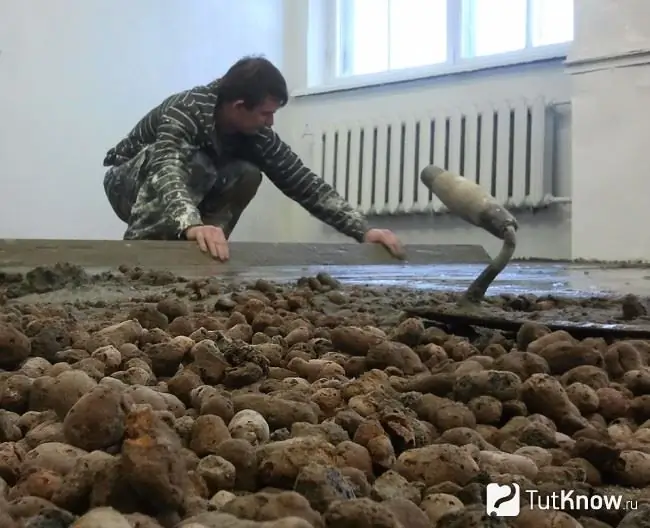
As for the fractions of expanded clay for floor insulation, in order to achieve greater efficiency, it is necessary to mix heterogeneous, that is, different sizes of granules. Therefore, large pieces of material alternate with small pieces in the same space. This is also due to the fact that large granules are worse compacted by themselves.
The very essence of floor insulation with expanded clay comes down to the following:
- Before falling asleep on the floor of the granules, it must be waterproofed. For these purposes, even ordinary plastic wrap can work. The joints on the panels are fastened with ordinary tape - this is necessary in order to end up with a single canvas.
- To carry out insulation, it is required to obtain a perfectly flat surface of the site. To achieve its leveling, the level of the future floor is marked with construction beacons before filling. The first is installed at a distance of 2-3 cm from the wall. All subsequent ones are placed in a parallel line, thereby achieving a single screed. You can use cement mortar to fix the beacons.
- After all the guides are aligned, proceed to backfilling the expanded clay granules. The layer of insulation should be as even as possible, not contain irregularities and drops.
- In order for expanded clay to be reliably fixed, it is poured with cement mortar. It will give the future layer the necessary strength.
- In some cases, the use of a reinforcing mesh may additionally be required. She will be able to give the whole structure a single whole and reduce the risks of deformation of the insulated coating.
The full hardening period of the poured floor is from 7 to 10 days, after which it will be possible to move freely on it.
Pouring concrete screed
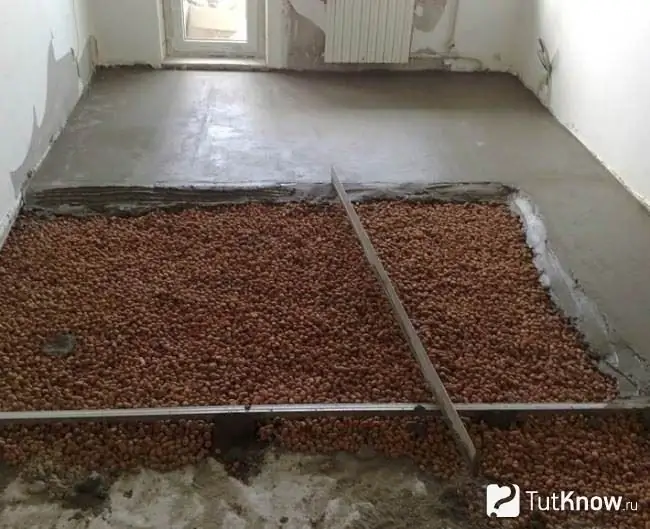
After the expanded clay insulation is laid, it must be closed with a concrete screed. It will not only give strength and fix the top layer, but also provide waterproofing on top.
But first, another intermediate layer is poured. It is made on the basis of a mixture of cement and water, which form a kind of suspension. It should be neither too liquid nor too dry. This layer is necessary for the cement to displace air from the air pores. The result is a monolithic coating that will not be afraid of heavy loads or excessive moisture.
But now you can proceed to the final screed, which will not only level the insulated floor, but also prepare it for laying any kind of floor covering.
The quality and strength of the entire structure as an assembly will depend on the quality of the prepared solution. In other words, it is the quality of sand and cement, as well as their proportional ratio in the mixture. A lack of cement leads to a weakening of strength, while an excess of it leads to an overly rapid solidification of the solution.
The optimal ratio is considered: 1.5 parts of cement to 1 part of sand, while water should be no more than 20% of the resulting volume of dry matter. It is added by eye, and then mixed until a homogeneous solution is obtained, which is poured onto the expanded clay on top.
The coating is leveled evenly over the entire layer of the heat insulator using a large spatula, and as a result, a so-called "tightening mirror" is formed.
The following guidelines will help you to create a correct and effective screed that will perfectly level the floor:
- It is important to prepare the potting mixture in the required proportion.
- Drafts, excess moisture should be eliminated whenever possible.
- The mixing plant and working containers for solutions should be prepared in advance, as well as ensure the functionality and safety of the equipment.
- The base level of the floor is measured, after which calculations are made to determine the height of the future screed.
- The layers must be applied in a sequential order.
- In order to control cracks, cuts with a spatula can be used if necessary.
The technology of floor insulation with expanded clay with the subsequent installation of the screed requires full drying of the poured surface before final finishing. This allows you to provide the necessary connection of materials. To do this, it must be covered with any protective materials - sheet cardboard, plastic, etc. will do.
Finishing of the insulated floor
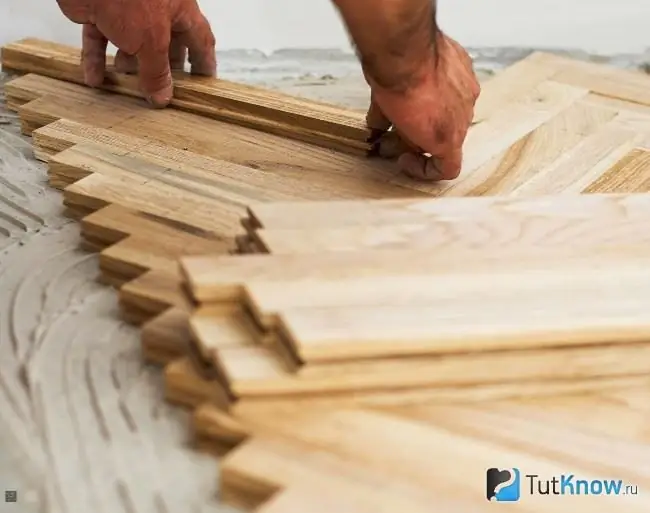
One of the promising options for finishing a heat-insulated floor can be the laying of parquet with subsequent varnishing. True, this technology is not affordable for every owner because of the high cost of wood. For parquet flooring, it is necessary to invite experienced craftsmen, as this requires special grinding machines and laying skills.
To give a finished look to the laid parquet, it is scraped. Skirting boards are mounted, the coating is coated with varnish or oil. Parquet scraping with subsequent sanding takes place in several stages using machines equipped with various attachments. For example, rough processing is used to eliminate differences between adjacent parquet boards, as well as to remove dirt. After that, sanding is done clean, as well as the processing of hard-to-reach places, in particular under the elements of the heating system, etc.
Lacquered and painted skirting boards are nailed to the walls after giving them their final look: wallpapering, painting, paneling. Skirting boards are nailed with special nails, which are driven in and hidden in wooden corks.
The final stage will be the finishing of the parquet. It can be varnished or oiled. This layer not only gives the floor an attractive appearance, it reliably protects it from moisture, household pollution and other influences that lead to accelerated wear of the parquet. Parquet boards cannot be washed without varnish or oil, but after coating, excess dirt and dust can be easily removed from them with a damp cloth. When working with parquet, it is necessary to use protective equipment such as masks and a respirator, and the doors and windows themselves in the room must be open for high-quality weathering of harmful fumes. Wait time between varnishing operations.
As soon as the first layer is dry, the surface is thoroughly smoothed with sandpaper. The dust must be collected with a vacuum cleaner and dry rags, after which a secondary varnish coating occurs. After it dries, the product is applied for the third and last time.
During operation, the lacquer layer gradually wears out, becomes covered with cracks and scratches. Therefore, it must be restored every few years. It is enough to cover the most worn-out areas of the parquet with oil, but in the case of varnish, it may be necessary to scrape with the removal of dirt and remnants of the old varnish. How to insulate the floor with expanded clay - watch the video:

Despite the fact that expanded clay has been widely used for insulating buildings several decades ago, it is still one of the most demanded materials today. This is due to the fact that in many qualities it is ready to compete even with high-tech modern heat insulators. In a word, according to standards and regulations, it is quite worthy to be used for various types of premises.