Porcelain stoneware flooring, material properties, types, selection and installation technology. Laying porcelain stoneware is the process of creating a decorative coating. Floor tiles made from this material have recently become a universal favorite among piece cladding products. This is due to the interesting combination of its aesthetic and functional characteristics. You will learn about the types, properties and technology of laying porcelain stoneware on the floor with your own hands by reading this article.
Technical characteristics of porcelain stoneware
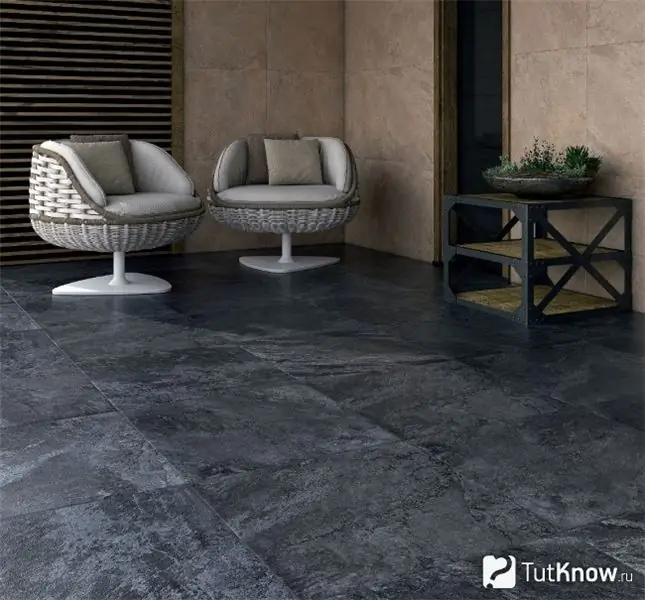
Porcelain stoneware is an artificial material. It is obtained by the method of semi-dry pressing under a pressure of about 500 kg / cm2 homogenized powder, which includes clays, pegmatites, quartz sand and feldspars. Then the products are fired at a temperature of 1200-1300 ° C.
To a certain extent, the production of this material can be considered a model for the formation of igneous rock occurring in the earth's crust. Therefore, ceramic granite is today considered a worthy substitute for a natural mineral.
The unique properties of this material make it possible to use it for external and internal cladding of building envelope structures. The appearance of the tiles, their rich range of colors and textures allows to implement many design solutions for flooring, facades and interiors. Porcelain stoneware, laid according to the correct technology, adheres perfectly to the floor and walls for a long time.
The material has extremely low hydrophobicity - less than 0.05% by weight. For comparison: for natural granite this figure is 5%. The frost resistance of the cladding is a consequence of the low moisture absorption. However, the low hydrophobicity of porcelain stoneware floor tiles leads to their flaking if the facing is carried out at sub-zero temperatures on a cement mixture. Therefore, such laying of the material is recommended only indoors, and outside using special glue instead of the usual solution.
Thanks to advanced production methods, porcelain stoneware has other advantages. These include:
- Material hardness … The absence of voids, microcracks, extraneous inclusions and the density of the structure make the tile extremely resistant to mechanical stress, the material is able to withstand a fracture force of up to 0.5 tons.
- Abrasion resistance of tiles … Some of its types are classified as class V on the PEI scale, which is the most durable material for this indicator, which makes it possible to use porcelain stoneware for floors in rooms with a high level of pollution and high traffic flow. Such facilities include supermarkets, train stations, airports, post offices and many others.
- Water resistance … The hydrophobicity index of ceramic granite is only 0.05%. For this reason, tiles have no equal materials among natural stones or other facing ceramics.
- Ecological cleanliness … Thanks to the natural components of the composition of raw materials, the tiles do not emit toxic substances that can negatively affect human health. This does not happen even with strong heating.
- Frost resistance … The high density of the material determines its resistance to negative temperatures. Therefore, porcelain stoneware can easily withstand frosts up to 50 ° C.
- Color consistency … When making tiles, the pigment is applied directly to the working mixture and evenly distributed throughout the entire thickness of the product. Therefore, the wear of the top layer of the coating during long-term operation will absolutely not affect its uniformity and color.
In addition, porcelain stoneware is inherently resistant to a chemically aggressive environment, resistance to temperature extremes, the so-called "thermal shock". It is possible to manufacture tiles with a structured surface with anti-slip properties. This is especially true when laying coverings on the street.
The maximum thickness of porcelain stoneware flooring is 30 mm. However, this indicator practically does not affect the strength of the coating. If the cladding is made in compliance with all the rules for laying the material, tiles with a minimum thickness of 3 mm will not be less durable than the same, but with a thickness of 30 mm.
The main varieties of porcelain stoneware for the floor
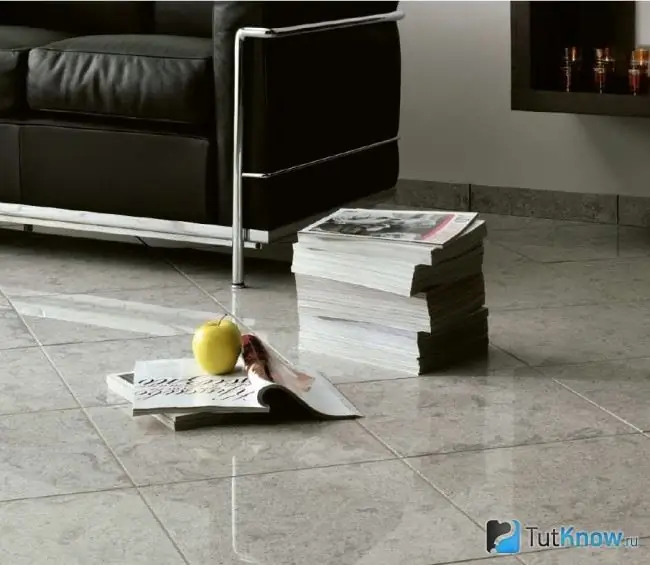
If you need to purchase ceramic granite for flooring in the hall, corridor, kitchen, bathroom or garage, first of all you should know its types, there are several of them:
- Technical porcelain stoneware … Outwardly, it resembles its natural counterpart. The material is seemingly undemanding, but it is relatively cheap, technologically advanced and can retain its original qualities for decades even with intensive abrasion of the floor with your feet.
- Polished porcelain stoneware … Such a tile has a mirror shine and looks very impressive, but due to the complexity and duration of the polishing process, it is more expensive than matte stone. Over time, as it wears off, the thin glossy layer coarsens and becomes matte. This process is accompanied by the opening of the pores of the material, until then closed by polishing. They get dirt, so polished ceramic granite is varnished during production. This procedure is often absent. In such cases, immediately after tiling the floor with porcelain stoneware, it is recommended to cover it with wax, varnish, etc.
- Matt porcelain stoneware … It does not undergo any additional processing and retains its texture acquired after firing. The modest appearance of matte tiles is fully compensated for by their high hardness.
- Glazed porcelain stoneware … During the production process, glaze is applied to this material and set during firing. Such tiles are more reliable and stronger than ordinary ceramic tiles, but it is still better to use them where mechanical stress on the cladding is minimal. Glazing gives a realistic imitation of ceramic granite marble, wood and other natural materials.
- Satin-finished porcelain stoneware … Before firing, mineral salts are applied to the surface of such a tile, and it becomes slightly shiny, but not slippery. The outer side of the product is decorative and is not intended to withstand significant loads.
- Structured porcelain stoneware … It has an embossed surface. Certain types of this material can imitate natural parquet or natural stone. In addition, there is a tile "under natural leather" or "under the fabric". Structured granite is processed in a variety of ways, from pickling to gold leaf coating.
- Rectified porcelain stoneware … This is a tile with cut edges. When laying it in a seamless way, the effect of the coating is monolithic.
All of the above items are available in various sizes. The smallest size of porcelain stoneware for the floor is 5x5 cm, and the largest is 120x360 cm, but such slabs are often used not for the floor, but for facing facades. The most demanded tiles are 30x30, 45x45, 60x60 and 40x40 cm.
Features of the choice of porcelain stoneware for the floor
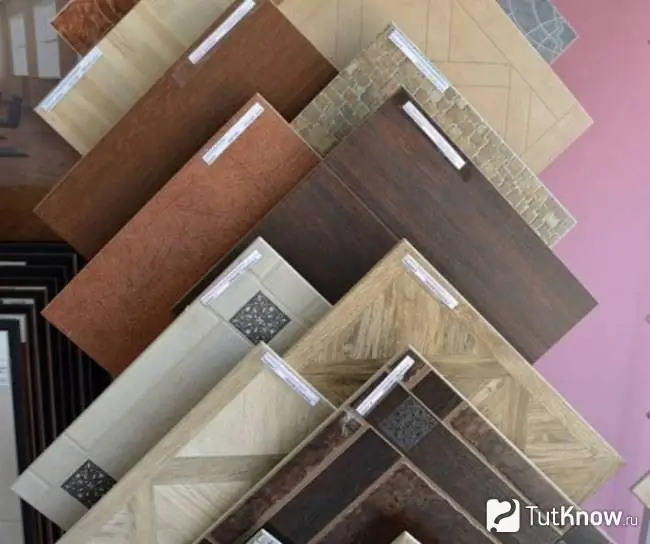
Ceramic granite is produced in the form of collections. Each of them includes tiles of a certain type. Therefore, to select it, you first need to familiarize yourself with the finished product catalog.
The purpose of the room, in which the ceramic granite flooring will be performed, and the interior design solution largely determine the choice of one or another type of tile. For example, for trade and exhibition areas, a relief surface of coatings is more suitable, for production workshops - antistatic or thickened technical porcelain stoneware, and for rooms with a high probability of contamination with oils or other aggressive substances - glazed material.
In addition, the choice of porcelain stoneware floor tiles is influenced by their format, thickness and weight. Let's take a closer look at the use of these indicators in this case:
- Tile format … This is its length and width. The selection of suitable piece sizes is important for two reasons. One of them is that small tiles are lighter than large ones, so they are easier to work with. But on the other hand, large porcelain stoneware creates fewer seams in the cladding, which then have to be rubbed. The next reason: laying large tiles with a size of 60x60 cm requires careful preparation of the base, and small tiles can be installed on a less even surface.
- Tile thickness … It is clear that the larger it is, the stronger the material. But its price is proportionally increased. To optimally choose a tile, taking into account its thickness, you should not overpay for the strength of the material with a "margin". The increase in costs will be justified only if the coating must bear increased loads in the form of installation of heavy equipment, machine tools and other things. For this purpose, in warehouses and production halls, when installing floors, a reinforced material is used, which is called "technical porcelain stoneware". And for train stations, terraces, shops and other civilian objects, similar tiles from home collections are quite suitable.
- Tile weight … Using ceramic granite in the interior, it should be understood that in terms of its characteristics, weight in particular, it is very similar to natural stone. The density of the material, which determines its weight and gives the tile excellent properties, at the same time imposes some restrictions on its use. For example, not every hardwood floor or interior partition can support the weight of the porcelain stoneware cladding.
The final stage of the pre-sale preparation of porcelain stoneware is its sorting by tone. The tiles that are most similar to each other are packed in one box. After that, the buyer's task is to select tiles of the same color for a particular room. Tone marking is indicated on the packaging with the product. It should be treated with attention, since otherwise it will be difficult to choose the required shade from any other batch of goods.
And finally, the last one. When choosing ceramic granite, you need to pay attention to the country of its manufacturer. Where the material is made matters a lot. The most expensive tiles are made in Spain and Italy. These products are considered elite, are distinguished by special elegance and use the most expensive and advanced technologies in their production. Ceramic granite from Turkey, China and a number of other European countries is cheaper. Russia also produces such tiles, and judging by the numerous favorable reviews, in terms of workmanship, it is not inferior to the products of most competitors.
Technology for installing porcelain stoneware on the floor
Correct laying of porcelain stoneware tiles on the floor is a rather troublesome task. It looks like a regular cladding, but has its own nuances. The installation of the coating consists of several stages, each of which must be carried out sequentially and technologically.
Floor preparation before cladding
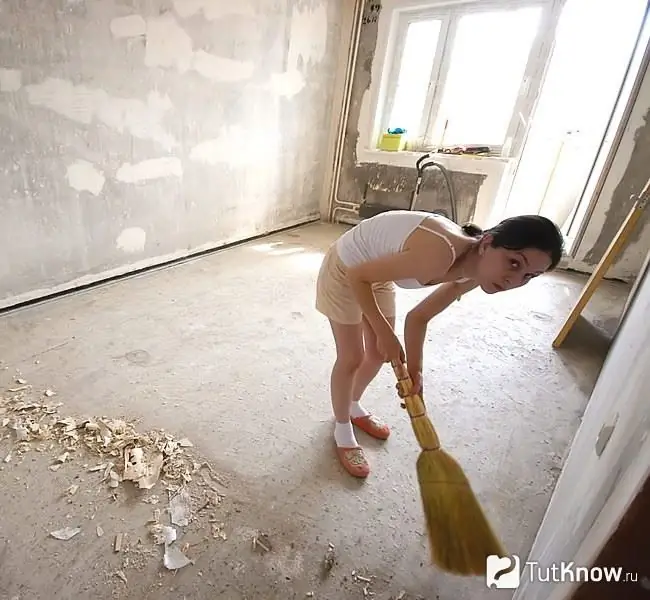
The main requirements for the substrate before laying porcelain stoneware are cleanliness, lack of moisture and an even surface. Therefore, before starting work, the floor should be cleaned of the old coating, remove mold, rust or grease stains from it, repair the cracks and gaps found, and then level and prime.
In case of significant differences in the plane of the floor, cement mortar should be used to level it. With small differences - self-leveling mixtures that create a thin screed by pouring it. Priming the finished base should be done 2-3 times after the floor has dried.
To install a wooden base for facing with ceramic granite, plywood sheets with a thickness of at least 12 mm or chipboard should be fixed on the floor logs. The joints between them must be sealed with wood putty, and then the surface must be primed and waterproofed. The adhesive for laying tiles on such a substrate must be elastic. Typically, such a composition includes epoxy resins or polyurethane.
Floor surface marking
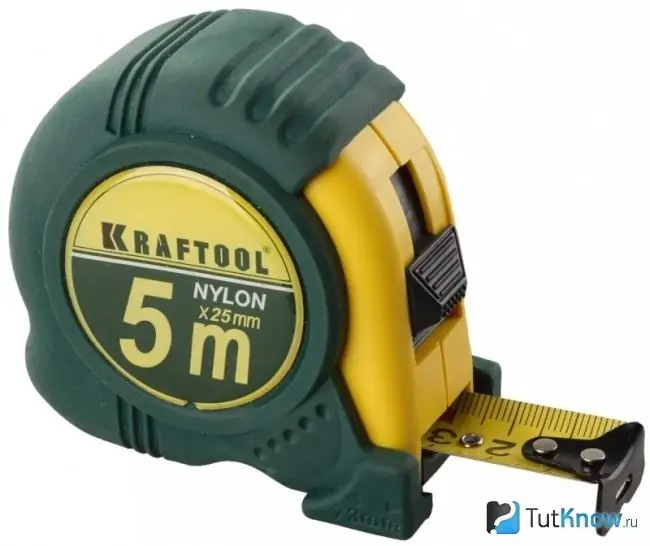
Before laying porcelain stoneware on the floor, it is necessary to choose the pattern of the future cladding. The arrangement of its elements affects the perception of the room space. A covering made of rectangular tiles visually lengthens the room, facing from small tiles visually increases its area, and from large tiles - reduces it. In any case, regardless of the floor pattern, porcelain stoneware will have to be cut at the abutments to existing structures or pipe outlets. Therefore, at the initial stage, when drawing up an installation scheme, it is necessary to determine how many tiles will need to be cut and what the dimensions of their parts will be during the procurement. Identical scraps of tiles can be placed around the perimeter of the room, forming a continuous row of them, and in the center of the room, lay a whole tile.
If you do not prepare the trimmed tiles, but simply start laying the floor from one of the walls, you should prepare for the fact that the symmetry of its pattern will be broken, since the trimming of the material will still have to be done near the opposite wall, but already in the process. If the size of the room allows you to fill its floor lengthwise or widthwise with rows of solid tiles without trimming, consider yourself very lucky.
If the base is already prepared for cladding, centerlines should be drawn on it for ease of use. It is best to use a coated paint line for this. First, measure the length of the walls with a tape measure and mark their middle on the corresponding sides of the floor.
After that, you need to pull the paint cord along the floor between the marks of the centers of opposite longitudinal walls and release it sharply. There will be a trace on the floor in the form of a flat center line. The same procedure should be done with the transverse walls. The intersection of two mutually perpendicular center lines will point to the center of the floor.
The tiles must be laid, focusing on this markup. With its help, it is easy to determine the dimensions of the parts of the tiles that will be located on the abutments. It is advisable to first try the prepared cladding elements dry on the floor and number them for further work with them.
Preparation of materials before installing porcelain stoneware
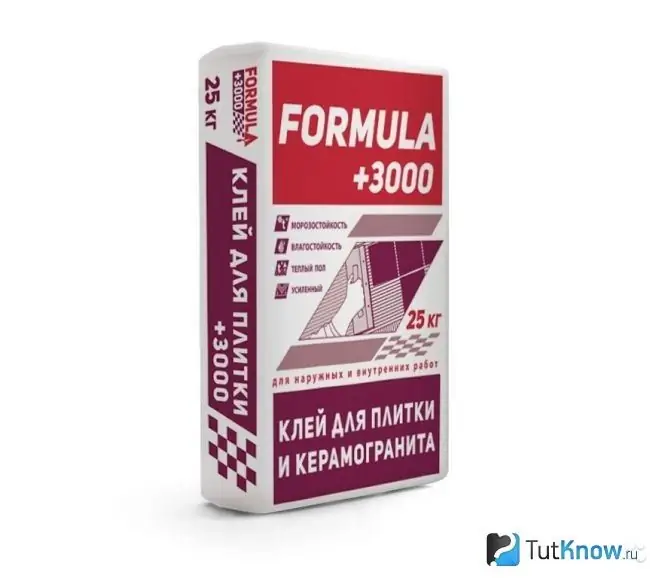
Before starting installation, it is necessary to remove the protective layer from the ceramic granite tiles, which is applied to the material by its manufacturers for safe transportation. Usually it is paraffin or technical wax. Paraffin can be easily removed with a spatula, and wax can be removed with cleaning agents designed to remove grease.
For laying ceramic granite on the floor, a special glue of increased strength is used. It contains a large number of polymer additives that provide this property to the composition.
After finishing the preparation of the base and tiles for installation, the dry adhesive mixture must be diluted with water in the proportion indicated on the powder packaging. Stirring the glue until smooth should be done with a mixer or a drill with a special attachment. The pot life of the finished mixture is from two to eight hours, so it is recommended to prepare it in batches.
Laying porcelain stoneware on the floor
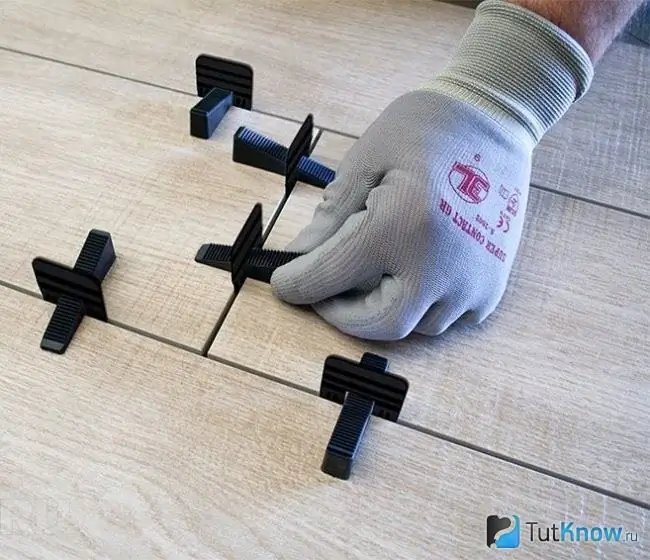
The main point that you should pay special attention to when installing ceramic granite is to eliminate the appearance of voids in the adhesive layer connecting the material to the base. Although such a tile is hard, it is quite fragile. Therefore, with an increased load on the product in the place of formation of a cavity not filled with glue under it, porcelain stoneware tiles can easily burst. To minimize this risk, the adhesive mixture is applied to both the base and the back of the product.
Apply the adhesive to the floor and spread it evenly with a notched trowel. The resulting grooves promote better adhesion of the cementitious material to the tiles. During installation, each product must be placed on an edge, and then carefully lowered by the surface plane onto the area of the floor treated with glue. In this case, the squeezing of glue from the seams between the tiles should be excluded.
The location of all cladding elements on the same horizontal level should be checked by the building rule. If necessary, you can slightly precipitate the tile with a rubber mallet, or vice versa - add glue under it.
In order for the floor covering to have the same seams, special dividing crosses are installed around the tiles, two on each side of the product. For porcelain stoneware, their thickness should be at least 3 mm. The adhesive under the tiles gains sufficient strength within 3-4 days.
After the end of this period, the crosses must be removed and the grouting of the facing seams must be started. Quality work is very important. The final appearance of the porcelain stoneware coating largely depends on it.
The grout joint should be selected in a color matching the design of the room. It is applied with a rubber spatula, carefully filling the lining seams. It is recommended to fill the joints of the floor to the walls or pipe outlets not with a joint, which can crack during vibrations, but with a silicone sealing compound.
After the fugue has dried, the tiles must be cleaned of traces of grout, glue and sealant. To do this, you can use a cloth soaked in water or a solution of any oxidizing agent. The installation of the cladding is completed by the installation of skirting boards.
How to lay porcelain stoneware on the floor - watch the video:
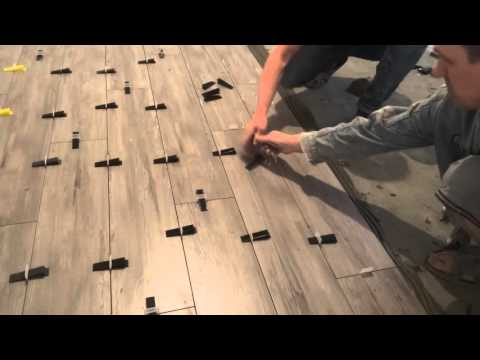
If you scrupulously observe the above-described technology for installing floors from porcelain stoneware, the result of high-quality work will be a reliable coating that beautifully imitates any natural material. Good luck!