Features of the use of liquid glass, the positive and negative aspects of the material, preparation of the ceiling for thermal insulation, insulation technology, decorating the treated surface with stretch fabrics. Ceiling insulation with liquid glass is a technology based on the use of silicate glue, which has become widespread both in industrial production and in private construction or repair work.
Features of the use of liquid glass
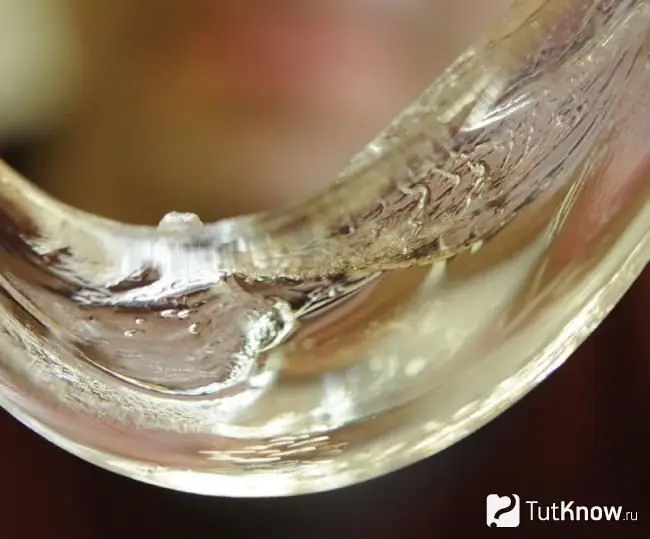
This material is a watery solution based on sodium silicate or potassium silicate, which are also found in traditional glass. Another name for it is silicate.
Water glass is produced by combining silicon dioxide with soda (potash), mixing it in an autoclave and melting it. No high-tech equipment is required for manufacturing. The manufactured products are crushed and dissolved in a water solution. During the production process, colorless or white crystals are obtained. Silicate is manufactured in accordance with GOST 18958-73 and technical conditions for products containing potassium TU 5921-001-63022882-2010.
Two types of liquid glass are made: sodium and potassium. Formula of sodium material (compound of two oxides): Na2O + SiO2; the modulus of silicate can be in the range of 2.0-3.5, and the density can vary from 1.3 to 1.6 g / cm3… Potash liquid glass has a modulus from 2.9 to 3.5, while its density is from 1.3 to 1.4 g / cm3… The main characteristic of liquid glass is its high thermal insulation properties. To achieve them, it is customary to combine this insulator with cement or concrete in a ratio of 1:10. This method is also recommended for facilities with excess moisture: bathrooms, saunas, garages, etc.
Insulation made of liquid glass is used as an impregnation to increase the thermal insulation qualities of ceilings, walls, floors, basements exposed to the environment or just water, for example, in swimming pools. When processing ceilings, first of all, it is necessary to talk about the protection of wood surfaces. This refers to wooden buildings - previously erected or modern buildings.
Scope of use of silicate:
- Thermal insulation and waterproofing works, they treat the walls and ceiling in the room and thereby protect them from heat loss and moisture penetration.
- Priming of surfaces (wood, stone, concrete) - before plastering or pasting wallpaper, they are covered with silicate.
- The material is used as one of the components for preparing a solution for laying stoves and fireplaces.
- It is used for the installation of linoleum, PVC tiles.
- Suitable for the production of putty for water pipes.
- It is used for the manufacture of acid-resistant and refractory silicate masses.
- Designed to protect foundations from groundwater.
- Potassium water glass is widely used in paint production, as it is resistant to atmospheric conditions.
The use of silicate is not limited to the above areas, it is an integral part of building materials such as putty, primer.
Advantages and disadvantages of liquid glass
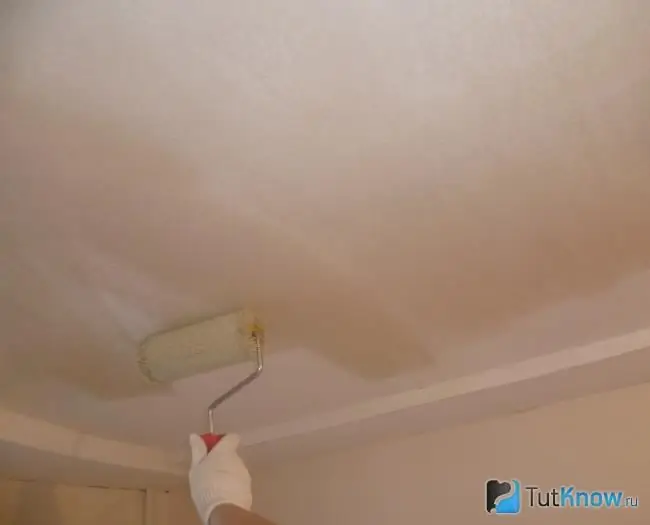
When the surface is coated with silicate, it combines with carbon dioxide contained in the air, as a result, it solidifies and fixes both its shape and size.
Surface treatment with liquid glass is popular due to the following material advantages:
- Extends the service life, gives the product strength.
- Creates a barrier to moisture penetration, as the insulator has excellent moisture-repellent properties. The surface treated with liquid glass will be protected from water for a long time.
- Possessing antiseptic properties, the liquid glass insulation protects the surface from putrefactive formations.
- The material is fireproof, resistant to combustion.
- Possesses high temperature resistance, can withstand temperatures up to +1000 degrees.
- Environmentally friendly for people and the environment.
- High fluidity - this property makes it possible for glass to penetrate into any irregularities, joints, both in wood and in concrete products.
- Low price.
- Low material consumption.
- Ease of use. These characteristics do not need explanation, because silicate is applied to the surface without much effort using a spray gun or a brush.
There are a number of specific weaknesses and disadvantages of liquid glass that need to be addressed:
- The base must not be treated with silicate if it will need to be painted in the future. The paint will not be able to lie on the surface to be treated, on which there is a film from the applied liquid glass.
- The scope of application is limited, this insulator can only be sprayed on surfaces with concrete, plaster or wood surfaces.
- Rapid crystallization of the material, so a certain skill is required to work.
Ceiling insulation technology with liquid glass
It is quite possible to make surface thermal insulation using silicate for both experienced builders and beginners. To do this, you have to get acquainted with the technological cycle and prepare the necessary materials and tools.
Rules for choosing liquid glass
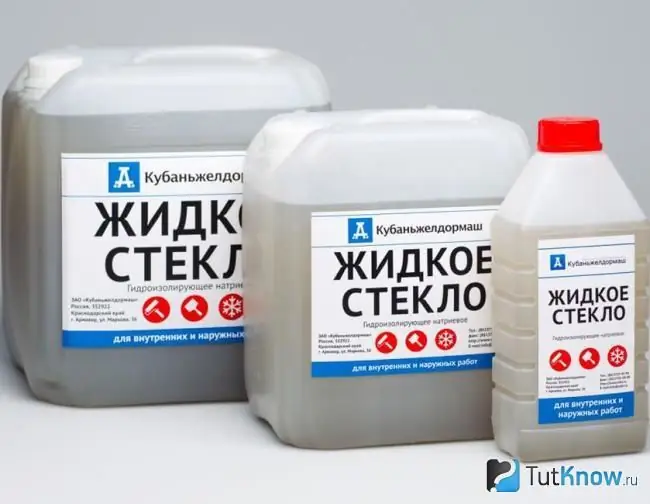
Manufacturers offer consumers the material in different forms: liquid or dry, in the form of powder or lump. Dry concentrate has its advantages in transportation, it is transported in bags. It dissolves in water and easily turns into silicate, it is only necessary to observe the proportions.
The main manufacturers of liquid glass in Russia:
- JSC "Kubanzheldormash" … The joint-stock company has been manufacturing products since 2007, with a production capacity of 300 tons per month. Produces high quality soda glass, being one of the main suppliers in the southern region.
- CJSC "Trading house" Stekloprodukt " … The products of this company from Ryazan are sold to more than 200 consumers on the domestic market. The material of this enterprise was used in the construction of Olympic sports facilities in Sochi. Products are manufactured in compliance with standards and production technologies.
- LLC "Metterra" … Produces exclusively liquid soda glass. The manufactured products of this company are in great demand among construction organizations and are an excellent offer on the market in terms of price and quality.
- LLC "Oxium" … It manufactures quality products, observing the GOST standards, however, an insulator with any characteristics can be produced at the customer's request. The products are in demand by construction organizations in the Ulyanovsk region, as well as in other regions.
- OJSC "Contact" … Produces a huge list of products. Among the customers are mechanical engineering enterprises that manufacture consumer goods. The undoubted advantage is that the enterprise produces not only liquid glass, but also powder glass, which is more convenient in transportation, does not require additional containers and does not freeze.
- JSC "Ivkhimprom" … The enterprise is successfully developing and is constantly working on the release of new varieties of glass, thanks to this, the production not only produces products, but also develops in its research center.
- NPO "Silicat", St. Petersburg … Despite the fact that the association was created recently, in 2009, it successfully conquers the sales market and expands the number of customers. It is engaged in the production of both liquid glass and silicate lumps. Since liquid glass is used as a connecting link in the production of electrodes, the association cooperates with manufacturers of these products.
You can keep such an insulator for up to 24 months. When stored at low temperatures, it can be exposed to frost, but if it is transferred to a warm room, its properties are restored. During storage, it may harden spontaneously.
If you need to implement fast and high-quality thermal insulation, it makes sense to pay attention to the liquid glass for the ceiling. After taking such preventive measures, it does not lose heat and does not let moisture into the room. This material can be used to treat any ceiling surfaces, especially wooden ones, since, in addition to insulating qualities, it significantly increases the fire resistance of the room.
Preparatory work
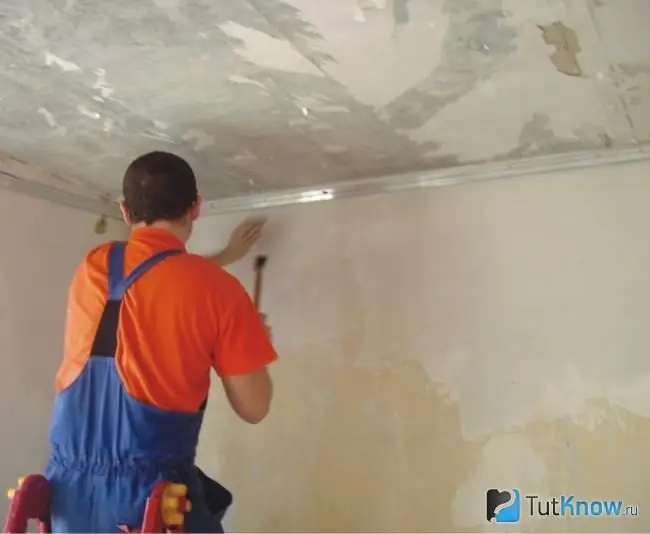
To begin with, the ceiling, which will be insulated, is freed from various contaminants. On the surface to be treated, we remove all irregularities, old materials with which it was processed. To do this, we use a spatula, and those materials that are difficult to extract can be obtained using a perforator.
If the ceiling was covered with water-based paint, it can be removed with a spatula, having previously soaked with iodine solution: 1 bottle per bucket of water. Before applying silicate, wooden surfaces must be thoroughly cleaned with an emery cloth.
The main tools with which the insulation is applied to the surface: spray, brushes or roller. You will also need a bucket, a sharp spatula, a puncher, a hammer, a screwdriver, a trowel, a level, a sharp cutter knife, a chisel, an emery cloth, a screwdriver, an aluminum or plastic profile, a gun for tensioning vinyl ceilings.
Prepare rubber boots, gloves, special glasses, an apron - protective equipment is necessary, since liquid glass has an alkaline reaction. In addition to the liquid glass itself, you will need such materials for thermal insulation: concrete, sand, water, stretch ceiling (final finishing material). After all the preparatory work has been completed, a heat-insulating layer can be applied.
Instructions for applying liquid glass to the ceiling
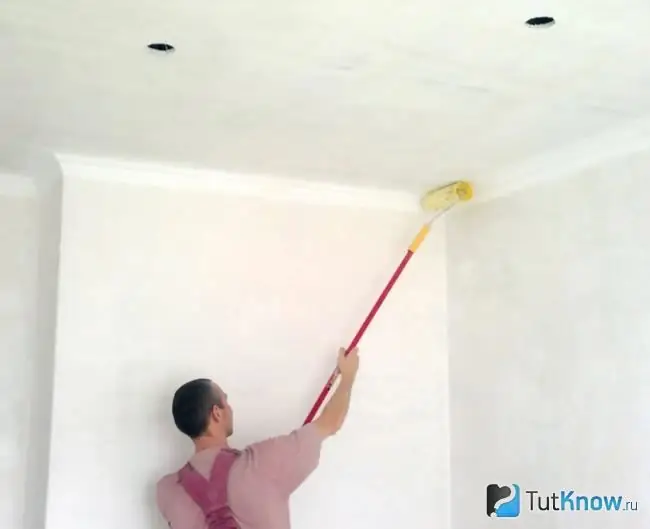
Silicate glue is applied to the ceiling with a spray gun, roller or brush, it all depends on the type of work. If a spray is used, then a suitable solution of water and silicate must be prepared in a ratio of 5: 1. The prepared silicate composition during surface treatment must necessarily have a room temperature. The final result depends on how competently the proportion of the components of the solution is observed.
The algorithm for carrying out the work itself is as follows:
- The heat-insulating mortar is applied to the surface with a brush or roller, it is carefully leveled, it is absorbed approximately to a depth of 1-2 mm.
- The insulation is allowed to dry for 30 minutes and a second layer is laid. To provide a deeper impregnation of the material, it is necessary to apply several layers of liquid glass, then the impregnation can reach 20 mm in depth. Prepared solutions from liquid glass must be produced quickly, as they tend to harden.
- Then a protective layer is evenly applied to the surface: a solution of liquid silicate with water is prepared in a ratio of 1:10 or 1:15, after which the prepared composition is poured into a concrete-cement mixture and thoroughly stirred. Constant stirring of the solution is prohibited, since the crystallization process is disrupted and the material loses its quality.
- Using a spatula, the solution is applied to the seams and cracks. For a good connection, the surface can be wetted. The solution is poured over the entire ceiling and waited until it dries.
Due to its flowing property, liquid glass penetrates into all irregularities and crevices, thereby protecting the treated area from the penetration of water and air.
After completing the thermal insulation on the ceiling, after 24 hours, you can decorate the surface, for example, install stretch ceilings.
Finishing the ceiling
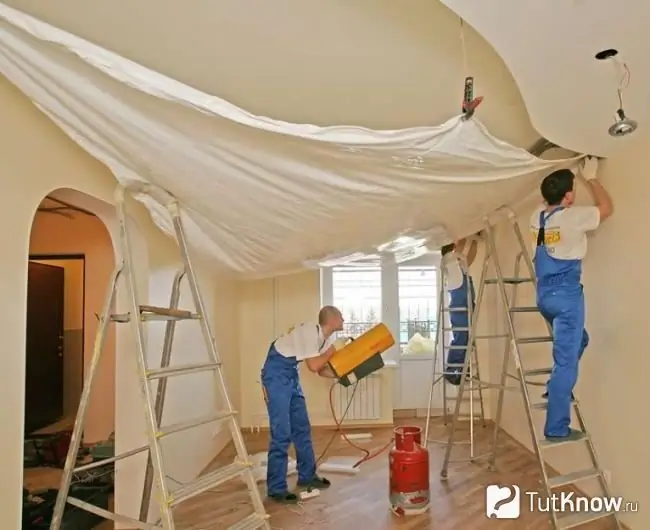
It remains to consider the finishing of the insulated ceiling, which can be decorated with stretch panels. The use of such a material allows you to hide all surface irregularities and aesthetically complete the composition in the room. Stretch ceilings in a city apartment create the effect of airiness and volume, and also protect it from moisture from adjacent floors. The consumer can choose up to 300 colors of the film with various effects - wood, marble, mirror, fabric, as well as a matte surface.
The mirror properties of the glossy ceiling allow you to visually enlarge the room, but the joints are clearly visible on them. Matte - classic products, not flashy, fit well into the interior of the room. Satin ones combine the properties of the above ceilings, the smooth surface of which allows you to increase the reflective effect. Vinyl panels are made according to the size of the room, having previously measured it.
Fabric ceilings have a different advantage - their installation leads to the creation of an absolutely seamless surface. They are made of polyester or knitted fabric, treated with a polyurethane solution. Unlike PVC ceilings, textile ceilings are not made to order, but sold in rolls, approximately 5 meters wide. Textiles are durable, easy to decorate and easy to install.
Before inviting specialists who will be engaged in the installation of the canvas, we recommend that you familiarize yourself with the following recommendations:
- The design of the stretch ceiling is selected after the choice of wallpaper and paint.
- You should not save money on the purchase of expensive and proven products on the market. Imported panels are much more reliable and durable than domestic ones.
- Check the availability of international certificates from the manufacturer of the products.
- The aluminum-based fastening system, which is needed to install vinyl structures, is much stronger than plastic.
- The choice of the type of ceilings (PVC or textiles) will depend on their advantages and disadvantages, as well as on the interior of the room.
Installation of vinyl and textile stretch ceilings is the same, it differs only in the order of work: vinyl is pulled from the corner to the center, and fabric, on the contrary, from the center to the corners.
Any stretch canvases should be in good harmony with the interior of the room, therefore it is recommended to entrust a specialist not only to fasten the material to the ceiling, but also to create a color scheme on the surface. After completing the installation, you can start installing lamps in them. For this, it is recommended to use halogen, fluorescent or conventional incandescent lamps. When mounting lamps on the ceiling, you need to know that the power of fluorescent devices should not exceed 60 W, and halogen ones - 20-35 W. Stretch ceiling maintenance is not very difficult. During operation, vinyl structures are washed with a cleaning solution that is removed with water. You can use a glass cleaner for wiping. Under no circumstances should you rub with scrapers, sharp objects, use abrasive cleaning agents that can damage the material! Textile ceilings are cleaned with a vacuum cleaner or brush.
How to cover the ceiling with liquid glass - watch the video:
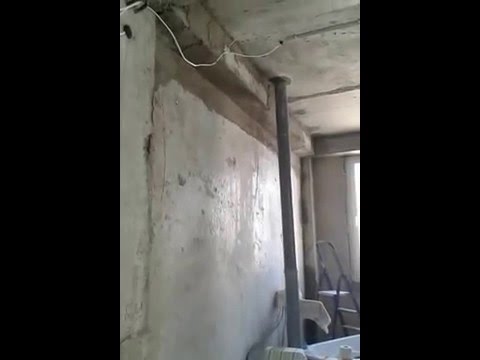
Thus, ceiling insulation with liquid glass is a well-proven method in construction, suitable for many types of buildings. It is carried out in a short time and does not require large material investments.