An article about methods of facade insulation using mineral wool, types of materials, characteristics of thermal insulation, its properties and features. Minvata is a material for thermal insulation, combining heaters made from rocks, blast furnace slag or glass melts. Due to its stable characteristics, it is widely used in construction. Today you will learn about the insulation of facades with mineral wool from our article.
Characteristics and types of mineral wool
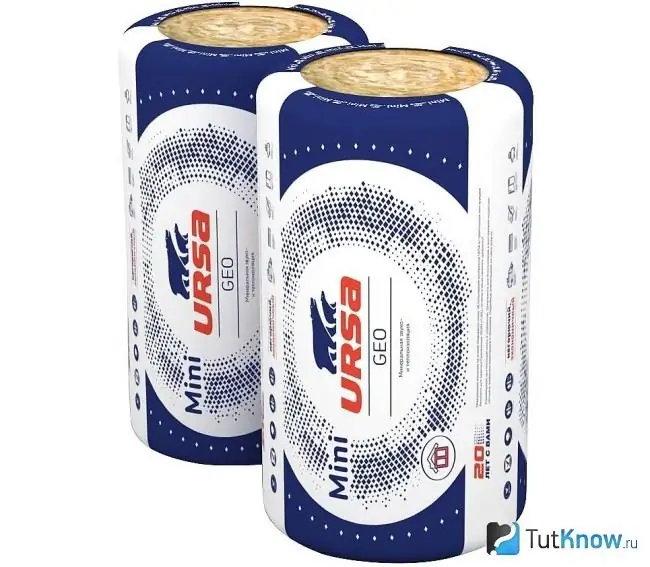
According to the material of manufacture, mineral insulation is divided into three types: slag wool, stone wool and glass wool. Depending on the feedstock, the products can have different fiber content, presented in a vertically layered, spatial, corrugated or vertically layered structure. This can affect the methods of wall insulation, leaving their essence unchanged.
Mineral wool is available in rolls and mats. The thickness of the material of both types is 40-200 mm, the width of the rolls is 600 and 1200 mm, the size of the mats is 1000x600 mm. The density of the insulation is from 30 to 100 kg / m3… Mineral wool can be supplied with an aluminum layer glued on one side of the material, which significantly increases its performance, both in terms of thermal insulation and in terms of moisture resistance.
Modern mineral wool is distinguished by a sufficient level of heat and sound insulation, high air permeability, resistance to vibration loads and an affordable price. The service life of this material without losing its heat-insulating properties can exceed 40-45 years. Minvata is a non-flammable and environmentally friendly material. Products can be easily laid on any surface, however, due to their high hygroscopicity, they need protective waterproofing. Soaked material quickly loses its properties and can become a source of reproduction of microorganisms.
Depending on the raw materials, each of the types of insulation has its own installation features:
- Glass wool … The insulation layer made on its basis is distinguished by its special elasticity and high strength. When laying it, you should use personal protective equipment for the skin and eyes: special glasses, thick clothing and work gloves to avoid getting microparticles of glass on the body.
- Slag … Due to its excessive hygroscopicity, insulation with this material is not suitable for metal surfaces, but it is suitable for facades made of wooden beams.
- Basalt (stone) wool … A distinctive feature of facade insulation with this material is the ability to work with it without personal protective equipment. Compared to other types of insulators, basalt wool has the best characteristics.
Advantages and disadvantages of mineral wool insulation
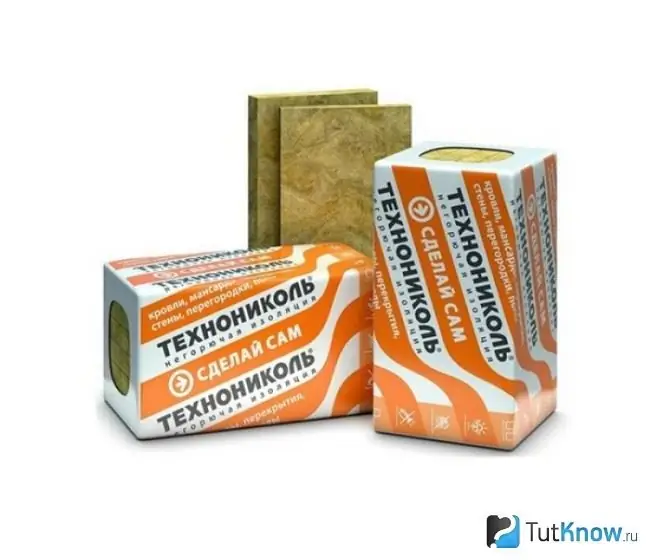
The advantages of thermal insulation of facades with mineral wool are:
- Excellent insulating properties of the finished coating.
- In the event of a fire, the insulation does not ignite and does not even melt at temperatures below 1000 degrees.
- Due to the sufficient hygroscopicity of the material, the surface does not accumulate condensation on the walls.
- Mineral wool insulation is soundproof, thanks to its porous structure, the coating perfectly absorbs noise from the street.
- Compared to foam, mineral wool insulation is more resistant to mechanical stress, which increases its service life.
- Thermal insulation with slabs allows the material to be in close contact with the base surface of the facade, and in rolls it can bend around the corners of the building during thermal insulation without leaving seams.
As for the disadvantages of mineral wool insulation for the facade, there is an opinion that the insulator contains carcinogenic substances that can negatively affect the health of people and pets. However, all heaters are tested in specialized organizations that supervise the quality of such products. Therefore, in order to minimize the risks from its use, it is recommended to buy mineral wool from trusted manufacturers, follow the rules for its installation and further operation of the coating.
Facade insulation technology with mineral wool
The work of insulating the facade with mineral wool involves a number of sequential operations, each of which is very important for obtaining a high-quality result. Let's consider them in detail.
Preparing walls for the installation of mineral wool
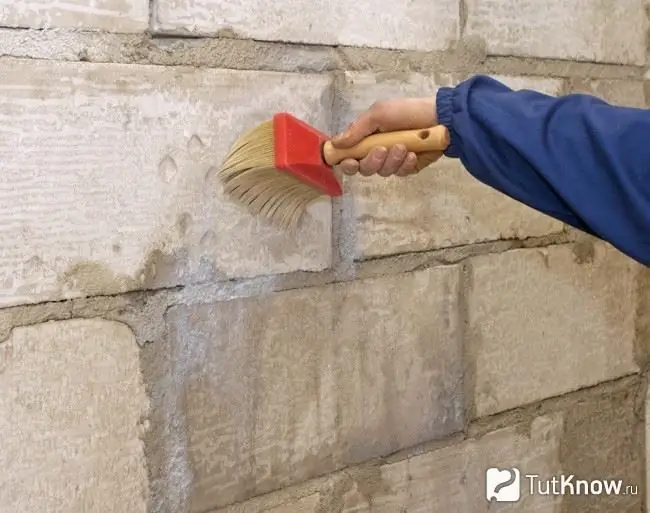
At this stage, it is necessary to remove from the walls of the building everything that can permanently or temporarily interfere with the implementation of thermal insulation. These can be rain drain systems, air conditioners, ventilation grilles, as well as nails, fittings or corners protruding outward from the surface.
In addition, you should pay attention to the presence or absence of mold, mildew, peeling plaster, mortar overflows, salt and greasy stains on the facade. If they are found, it is necessary to take measures to eliminate these defects.
After cleaning the walls, it is recommended to cover them with a primer, which can be applied with a large paint brush. If there are traces of mold on the surface, they must be treated with an antifungal agent. It is advisable to protect the joints of the abutment of the walls to the basement of the house with a water-repellent compound.
In order to evenly fix the mineral wool slabs on the facade, the walls should be hung before installation. It is produced in horizontal, diagonal and vertical directions.
The work is carried out using a nylon cord, which should be alternately pulled between the pins pre-installed in the wall. Unequal gaps between the cord and the reference surface clearly show the curvature of the plane. If the relief drops are significant, it will have to be leveled. After checking, the pins should be removed.
Installation of the support profile is necessary to support the first row of thermal insulation, to establish a gap between the wall and the insulation. They are fixed horizontally to the façade above the plinth with dowels. The fixing of the guide strips is carried out around the entire perimeter of the house and is controlled by the building level.
In order for the surface of the insulation to be completely closed, under the guide profile, it is necessary to attach a reinforcing mesh in the form of a strip 250-300 mm wide to the glue, and then wrap its lower edge onto the bar when installing the rest of the mesh on the heat-insulating plates.
Choosing a method of fixing mineral wool
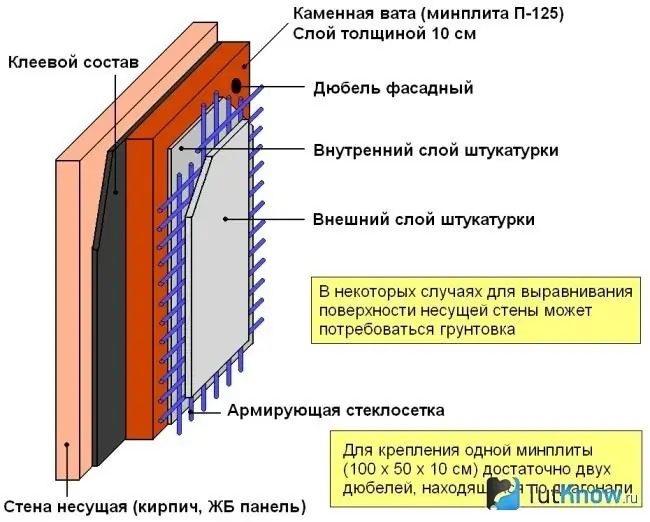
Mineral wool insulation is usually carried out under siding, stone slabs, facing bricks or facade plaster. Depending on the type of external cladding, the type of fastening of the heat-insulating material is selected:
- Facade plaster … Its most popular species today are "bark beetle" and "lamb". In this case, the insulation is glued to the base and additionally fixed with umbrella dowels. A reinforcing mesh, a layer of primer and a layer of plaster are alternately laid on it.
- Siding … With such a facade cladding, the insulator is located in the cells of a prefabricated frame fixed to the facade. After insulation, the siding panels are fixed on the crate.
- Facing brick … It fits in the same way as usual, from bottom to top. In this case, a layer of mineral wool is placed between the base surface and the external decorative masonry.
- Stone slabs … They are attached to the facade with metal anchors, pressing the insulation to the base surface. Special holes are made for the anchors in the wall, and then the stone slabs are fixed to these fasteners using insert hooks.
Instructions for installing mineral wool on walls

When installing mineral wool on the facade, the main and additional fastening of the slabs is used. In the first case, the insulation is fixed to the walls with a special glue, for example, Ceresit CT190. This is done in this way.
The dry mixture of glue must be diluted with water in the proportion indicated by the manufacturer on the packaging of the material. This procedure can be performed in a bucket using a construction mixer. Stirring should be done until a homogeneous pasty mass is obtained, after which it should be left for 10-15 minutes to “ripen”, and then mix again. This will give it greater plasticity and better adhesive properties. The performance of the finished glue is maintained for 2 hours.
When pasting the facade with insulation, it is recommended to apply the mixture to its plates with a notched trowel. This method of installing thermal insulation allows you to create a solid, strong and sealed layer on its back side, which can protect the product from penetrating moisture during work and further operation.
Installation of the first row of slabs is carried out on the support profile. They should be located evenly, horizontally in the same plane. Laying control should be carried out using a plumb line and a building level. The ends of the products should be joined without gaps, if gaps do appear, they should be sealed with thin strips of identical material. Vertical joints in each row of slabs need to be offset relative to each other, this will give strength to the thermal insulation coating.
In order for it to be also durable, the insulation should be additionally fixed on the facade with disc dowels. In this case, it is necessary to use fasteners with a metal core. To perform this work, you will need a hammer and a hammer drill.
Holes in the wall are drilled through the insulation plates, then umbrella dowels are driven into them, pressing the products to the facade. For installation 1 m2 the insulator takes 5-7 dowels if the height of the building is up to five floors. At a higher height, you will need 7-8 pieces of fasteners for each square meter. Dowels should be driven in at the corners of the slabs and in the centers.
Important! The indentations obtained in the insulation plates after installing the dowels must be immediately sealed with adhesive solution.
Reinforcement of the surface of the insulation
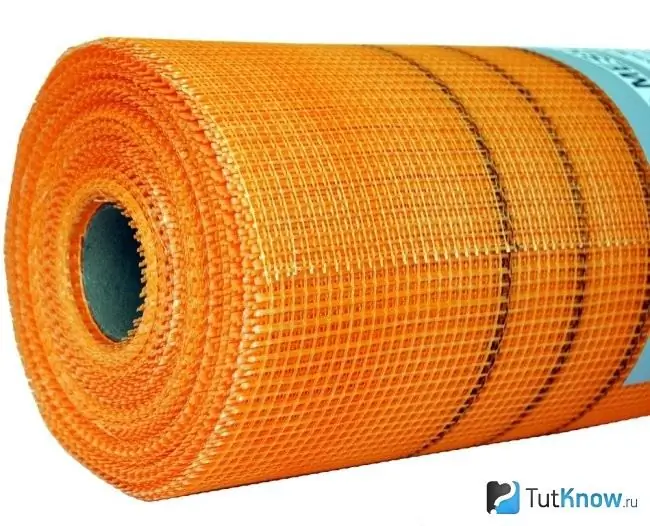
It has two goals: to strengthen the thermal insulation coating and to protect it from wind and moisture. This operation is performed using a reinforcing fiberglass or polyurethane mesh. For its installation, the material should be rolled out, starting from the top of the wall. The canvases must have an overlap of at least 100 mm. Before rolling out the mesh, a thin layer of construction glue must be applied to the surface of the insulating layer, and after laying it, the reinforcement must be covered with another layer of the mixture. Then it must be leveled with a rule and allowed to dry.
After 2-3 days, it is necessary to remove glue drips from the dried coating with a spatula, and then clean the surface with an emery cloth. After that, the insulated facade should be covered with a primer paint - and you can start finishing it.
Decorative finishing of the facade

Facade decoration with mineral wool insulation can be done with smooth or textured plaster. The topcoat is most often facade paint. In any case, when decorating external walls, the following rules should be observed:
- All materials used must be designed for outdoor use.
- The topcoat and plaster layer must be compatible, that is, if the plaster is acrylic, the same should be the facade paint.
- Exterior wall decoration must not be performed at low air temperatures, atmospheric precipitation or strong winds. It is also recommended to refrain from carrying out such work in bright sun.
- It is necessary to know that the application of some paint coatings requires preliminary treatment of the surface of the walls with appropriate primers. In particular, this applies to silicate and silicone paints.
How to insulate a facade with mineral wool - watch the video:
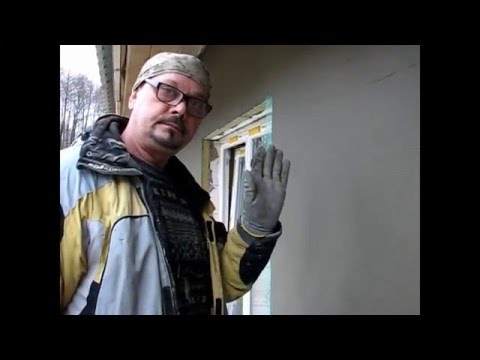
The cost of the above works without finishing with the involvement of professional builders will be about 670 rubles / m2… This price is by no means high, but if you want to save money, you can completely insulate the facade with mineral wool with your own hands. It is not difficult at all, and we hope that our article will help you in this matter. Good luck!