From the article you will learn how to make an artificial stone for wall decoration, about its properties and types, get acquainted with the technology of work, equipment and necessary materials. Artificial stone is a material obtained from a solidified mixture of various components. It has been known for a long time: hardened lime mortar, for example, or ordinary brick also refers to stones of this type. However, only in the modern world has an artificial mineral taken the lead in the creation of landscape design and decorative finishing of houses. The reason for this is the latest technologies and materials, thanks to which the production of decorative stone has become possible even at home.
The advantages of artificial stone
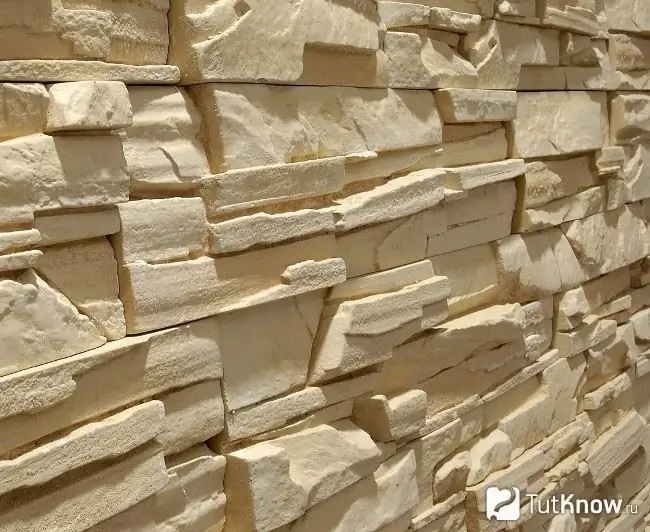
If we compare the two types of stones, it turns out that natural stone is a very expensive and rather capricious material. It is difficult to saw it with thin plates - it is too fragile, samples of large thickness are heavy and significantly load ceilings and walls when facing.
Another thing is artificial stone. In terms of its durability and mechanical properties, it is not inferior to its natural counterpart and can surpass it, even made by handicraft. In addition, artificial stone has important advantages:
- It can be produced in the form of thin tiles, which significantly reduces the weight of the cladding without losing its strength.
- It has a richness and uniqueness of colors and surface textures, can be manufactured according to standard sizes and shapes, or be shaped right at the place of installation.
- The material can be produced directly on site, eliminating waste in transit.
- It can be produced immediately with a shiny and smooth texture, which eliminates the cost of polishing and grinding.
- It can have irregular shapes, accurately imitating any stone, but of a predetermined configuration and size.
Externally, artificial and natural stone practically do not differ. But at the same time, the first is devoid of all the shortcomings of the second and can even imitate its texture. The surface of a decorative stone can have uneven edges in the form of chips, resemble a cut of a sawn mineral, or be arbitrary-decorative, giving room to the imagination of designers.
The main varieties of artificial stone
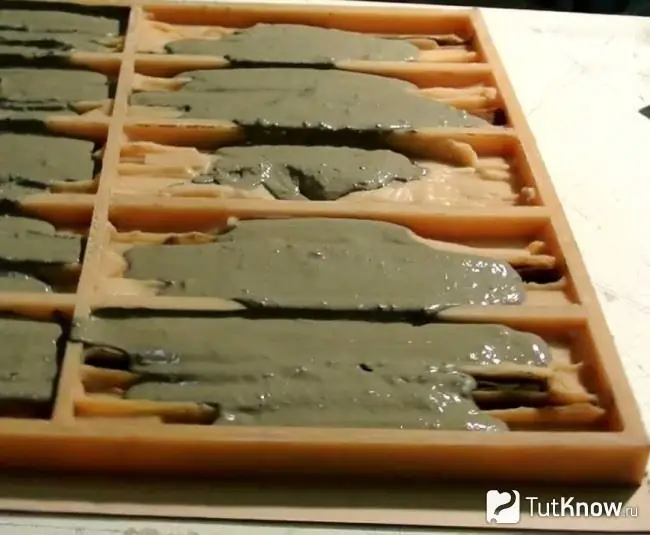
Artificial stone for walls can be made from a wide variety of materials and in a variety of ways. These signs divide it into types:
- Ceramic stone … It is made from clay by firing workpieces in a given temperature regime. Its manufacture requires significant floor space, high energy consumption and trained personnel.
- Gypsum cast stone … It can be made at home, the costs are minimal, but the material is suitable only for interior work, as it does not withstand low temperatures.
- Concrete molded stone … Its cost is slightly higher than that of gypsum, since concrete molds wear out faster. The stone can also be produced at home or in any utility room. Possesses good frost resistance, is produced at a temperature of +12 degrees and above.
- Polyester stone … In terms of mechanical and decorative qualities, it may even surpass natural counterparts, but the polymerization of the binder of the workpiece takes place in a vacuum at a high temperature. Therefore, such a stone is not suitable for home production.
- Acrylic cast stone … It is a cold cure material. It is suitable for home production in the same conditions as plaster. Its main advantage is chemical resistance and the absence of pores. In a domestic environment, this ensures hygiene and excellent sanitation. The combination of strength and toughness in acrylic stone makes it possible to make stone wallpaper from it. For on-site work, the stone can be made in the form of sheets with a thickness of 3-4 mm. Naturally, they require careful treatment, but having a suitable mold for casting, they can be produced to the full height of the wall. Prefabricated stone acrylic slabs are much thicker - 6, 9 and 12 mm, but this is necessary for their transportation.
The cost of these materials is low, but making an artificial stone with your own hands is even more profitable. The final price in this case will be significantly lower than the market price, and this will allow finishing large areas of walls at minimal cost.
It is not difficult to make such material at home. Success in this business depends on having a good casting mold. It is not worth saving on quality, so buying a cheap plastic mold that breaks after a small amount of fillings is not rational. Molds made of silicone or polyurethane are considered to be the most durable and reliable.
DIY artificial stone technology
In general, the entire production process consists of several stages. This is the manufacture of a model of a stone, a casting mold, pouring and molding of a mixture, the introduction of pigments and polymerization of the material to obtain a finished product. Let's take a closer look at each of the steps.
Materials and equipment for the manufacture of artificial stone
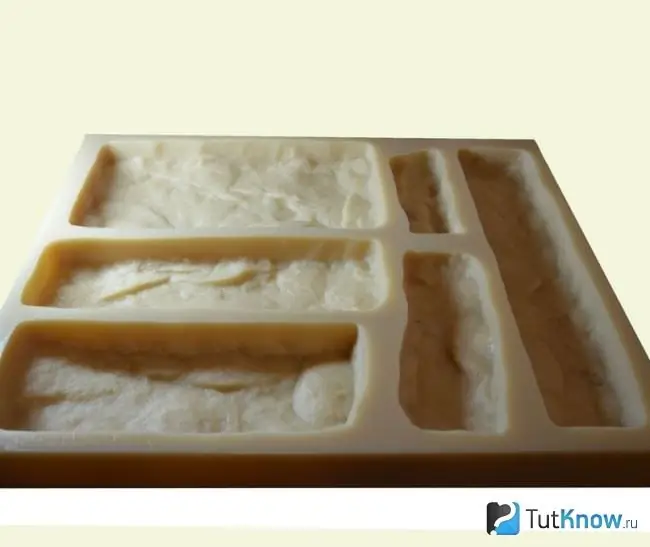
To make an artificial cast stone yourself with factory quality, you will need special materials and equipment:
- Vibration stand … This is the heart of the production of decorative stone, the quality of finished products depends on its correct operation. The design feature of the shaker ensures the homogeneity of the mixture during its polymerization. You can make it yourself. The stand is based on the principle of oscillation of its platform in a horizontal plane.
- Mold models … They are necessary in the absence of finished molding products.
- Release agent … This substance is applied both to the model during the production of the mold, and to the inner surface of the mold before casting the artificial stone. This procedure is performed in order to avoid adhesion of materials to each other.
- Foundry molds … Designed for storage of material during its polymerization.
- Foundry mixtures … They can be very diverse, ranging from gypsum to complex polymer compositions.
- Pigments … They give the stone a coloration to mimic natural minerals.
- Sand cushion pallet … It protects silicone molds from deformations that can occur during the stone production process.
- Thermal gun … This is a miniature hair dryer that produces a strong and thin jet of heated air during operation. The tool is designed for welding finished acrylic elements.
How to make a model for an artificial stone
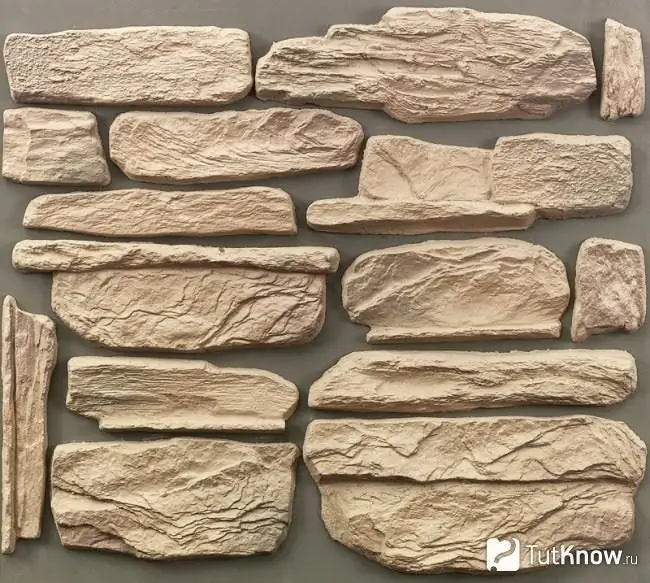
Prefabricated artificial stones or suitable natural stones can be used as models for making casting molds. In both cases, the set of surface reliefs, sizes and shapes of the final product is limited. However, literally underfoot almost everywhere there is an excellent material for the production of unique models - ordinary clay.
Its use for household needs does not require any permits, gully clay is not included in the number of minerals. Analyzes for impurities, fat content and the like are also not needed, as long as it is kneaded or molded.
Tile models for cladding are made using a grid made of strips of smooth and thin plastic. When choosing the height of the lattice, one proceeds from two options: for concrete and gypsum stone, it is taken equal to 6-12 mm and over 3 mm - for acrylic stone for liquid clay or 20-40 mm for clay with stucco molding.
In all cases, they take an even shield and cover it with PVC film, then install the grating and fill its cells with clay. For the location of the shield, a place is selected in advance, protected from the rays of the sun, otherwise, when drying, the model will be covered with cracks. Drying control can be done with a lump of clay stuck near the grate. The low grate is filled to the top with liquid clay. After drying, each tile obtained naturally takes on a unique relief. The high lattice is filled with a thick clay layer, the thickness of which is oriented to the final product.
The required relief is formed manually. On the surface, you can make bas-reliefs, inscriptions, magic signs, hieroglyphs, and more. Drying of such models takes place in the shade under a canopy and takes, depending on weather conditions, from two to five days. Its speed can be increased by hanging an infrared lamp with a power of 100-200 W above the models at a height of at least 2 meters.
Making a homemade mold for artificial stone
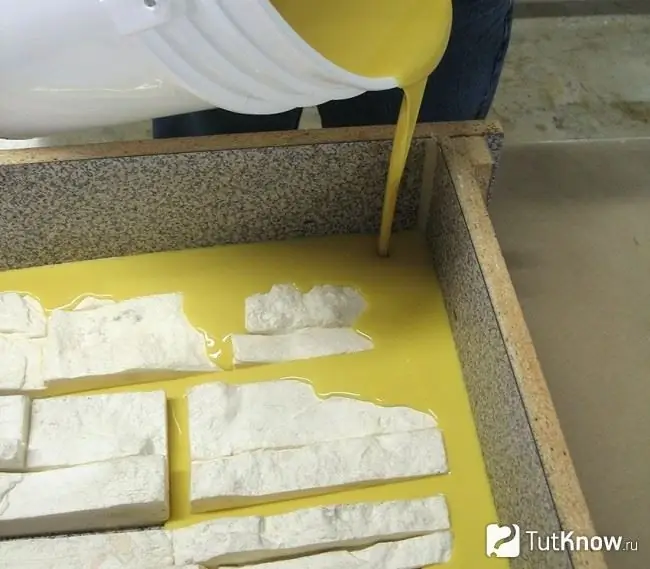
At home, homemade artificial stone molds can be made from silicone. To do this, the model or a whole set of them is laid on a flat surface covered with a film and surrounded by a small side, the height of which should be 10-20 mm higher than the level of the outer surface of the model. The inside of the fence and the models themselves are lubricated with a fatty substance: cyatim, grease or mine breaker.
The shield with the samples laid on it is installed in a strictly horizontal position to obtain a flat silicone surface, which in the future will become the bottom of the mold. To fill the structure, a cheap acidic silicone with a strong vinegar smell is chosen. It is squeezed out of the tube directly on the model, starting in a spiral from the middle to the side until the cell is filled with material. To eliminate the formation of bubbles, the silicone is spread with a flute brush, dipping it each time in a foamed dish detergent solution. Soap solution is not suitable for this purpose. It contains alkali, which can damage acidic silicone.
After filling the cell, the surface of the composition is smoothed with a metal spatula, periodically wetting it in a detergent. Drying of the mold is carried out in the same way as for the clay model, but without the infrared lamp, avoiding the appearance of bubbles. But airing the drying significantly speeds up. Silicone dries at a rate of 2 mm per day. To control the process, a ring filled with silicone is placed next to the forms. The resource of such products is about a hundred castings.
Preparation of mixtures for artificial stone
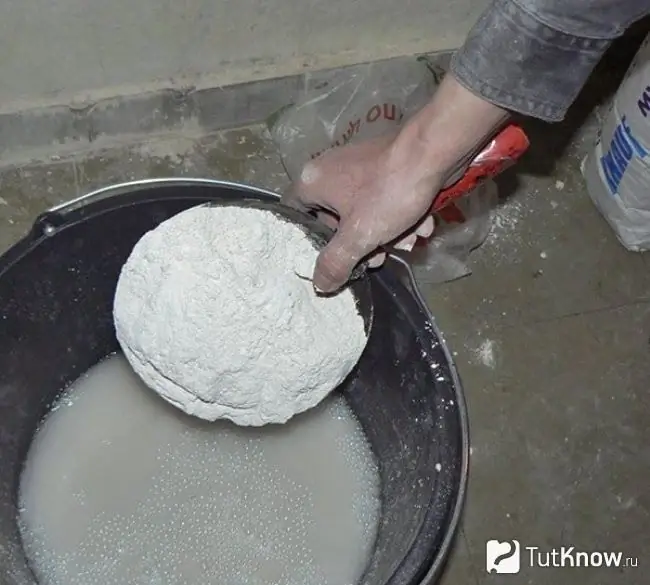
Artificial stone of each of the above types has its own composition of the working mixture required for the manufacture of the material:
- Concrete stone … It contains a cement-sand mixture in the base, but the ratio of its components differs from the proportions of the mortar in the opposite direction: one part of the sand accounts for three parts of cement. The addition of pigment is 2-6% of the weight of concrete, sometimes polymer additives are added.
- Gypsum stone … Due to the fact that the vitality of the gypsum mixture is about 10 minutes, it is prepared in small portions, which are enough for the production of one or several products. The composition of the solution includes: gypsum, water 0, 8-0, 9 of the volume of gypsum for the initial layer and 0, 6 for the rest of the mass. In addition, the mixture includes 0.3% by weight of gypsum citric acid and 2-6% pigment.
- Acrylic stone … It is based on acrylic resin and hardener. For the finished mixture, the proportion of the mineral filler with the pigment is 3: 1. The filler in the composition is gravel, stone chips or screenings. A decrease in its proportion increases the elasticity of the product, but decreases its mechanical strength. To prepare the mixture, the filler is treated with a detergent, washed, ignited, and then rinsed again in clean water. Then the pigment is introduced into the filler, then the acrylic resin is mixed with the hardener, the pigment with the filler is introduced and mixed again. The pot life of the finished mixture is 15-20 minutes, the setting time is 40 minutes, and the product is ready for a day.
For the production of artificial stone for walls, liquid, powder, synthetic and mineral pigments are used. Powdered pigments are added to dry gypsum or filler, liquid dyes are added during mixing. The pigment may have the consistency of a paste. With its help, a striped or spotted color of the stone is achieved: at the end of mixing, a paste-like pigment is injected into the mixture with a syringe.
Artificial stone casting technique
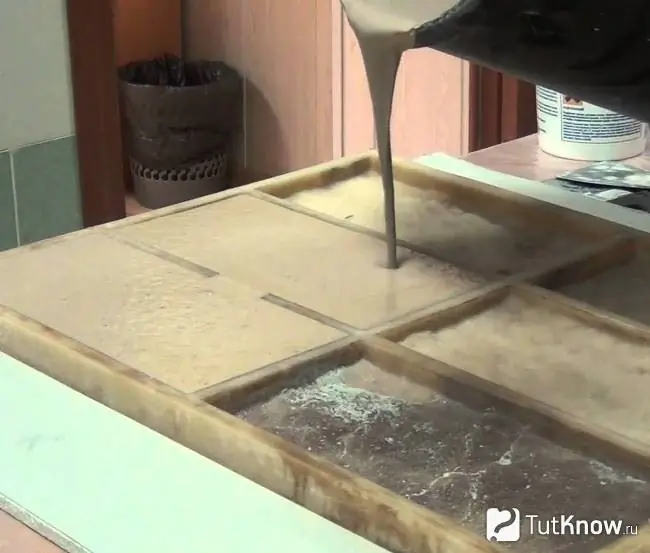
The technology of casting artificial stone provides for the basic and starting stage of work. Accordingly, to ensure quality and economy, a facial starter and base mix are made. When filling in small forms that do not have a relief surface, face mixes are immediately used. They are liquid, they envelop forms well, they have pigment and filler in their composition.
Such mixtures are applied to the mold with a brush. Sand with cement and gypsum for the starting mixture are diluted to a liquid consistency, in the acrylic mixture the proportion of the pigment with the filler is reduced to 60%, respectively, increasing the proportion of the resin with the hardener.
After polymerization of the starting composition, the mold is topped up with the base mixture. Microcalcite is used as a filler for acrylic. It provides a background against which the decorative properties of the facial mixture are perfectly manifested.
The basic plaster solution is kneaded to the consistency of sour cream. When pouring a concrete stone, the base layer is made in two steps: first, the mold is poured in half, then a reinforcing plastic mesh is laid, and then the mixture is poured to the edges.
After completing this procedure, using a spatula, smooth the base fill flush with the edges of the mold. At the beginning of the polymerization, grooves are drawn on the casting to increase the adhesion of the product with the binding material during the future facing.
During casting, the shaker must be turned off. After removing from the mold, the gypsum stone is treated with hot vegetable oil to increase resistance to external influences.
Watch a video about making artificial stone:
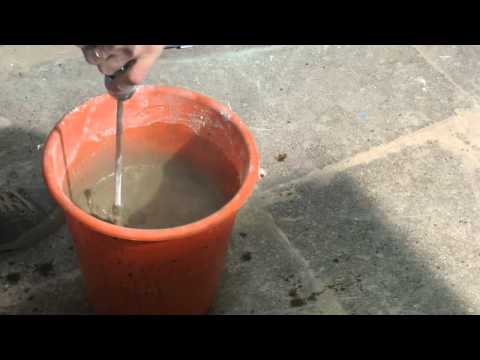
Before making an artificial stone, you need to decide on the type of wall decoration and the requirements for the material. If you need to make stone for interior wall decoration, give preference to plaster and acrylic. For outdoor work, you will need a moisture-resistant material. Therefore, in this case, the rational solution would be to use a concrete stone. As for the cost, the most expensive is acrylic material, then, in descending order, there is a concrete stone, and then gypsum. Good luck with your choice!