Thermal insulation of walls using liquid foam, its features, pros, cons and technology of work. Thermal insulation of walls with liquid foam is an easy and reliable way to create a comfortable indoor climate. The porous substance is effectively used for thermal insulation of building structures made of almost any material. You will learn how to insulate a house with liquid foam today from our article.
Features of thermal insulation of walls with liquid foam
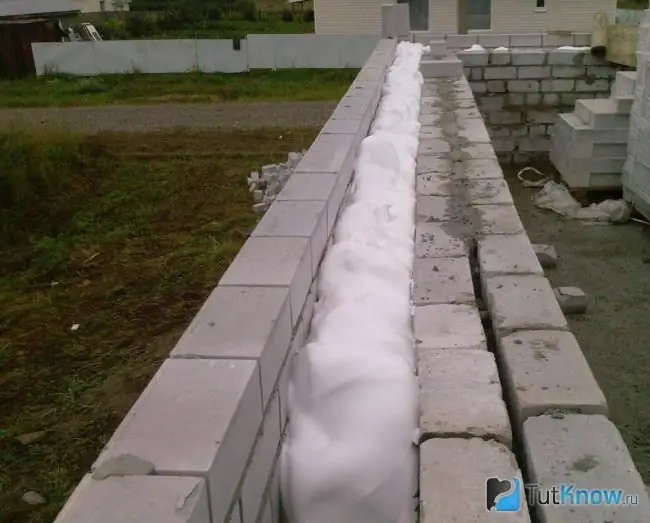
Liquid foam, aka Penoizol, is obtained by foaming urea-formaldehyde resin. It is noteworthy that the entire production process of thermal insulation is carried out directly at the facility: there the product is manufactured, supplied in a liquid state under pressure to the prepared cavities, fills them, and then hardens.
With such an organization of labor, there is a significant saving of money and time on transportation costs, storage of insulation, purchase of fasteners and performance of work related to their installation.
The resulting coating has a density of 10-30 kg / m3, excellent insulating properties and low thermal conductivity - 0, 028-0, 038 W / m * C. According to the latter indicator, Penoizol holds heat 2 times better than ordinary foam, while surpassing even mineral wool.
For clarity and proof of the effectiveness of house insulation with liquid foam, it can be compared with traditional insulation: a 10 cm thick layer of this material in terms of thermal insulation properties is equivalent to 30 cm of ordinary foam, 20 cm of mineral wool, 34 cm of wood, 90 cm of brickwork or 210 cm of concrete.
Liquid foam is used not only in new construction, but also as a material intended for the repair of thermal insulation areas destroyed during the operation of the building. Penoizol, for example, can fill cavities that have formed due to shrinkage of bulk insulation, its poor-quality filling, or those that have arisen in foam damaged by rodents.
Advantages and disadvantages of wall insulation with liquid foam
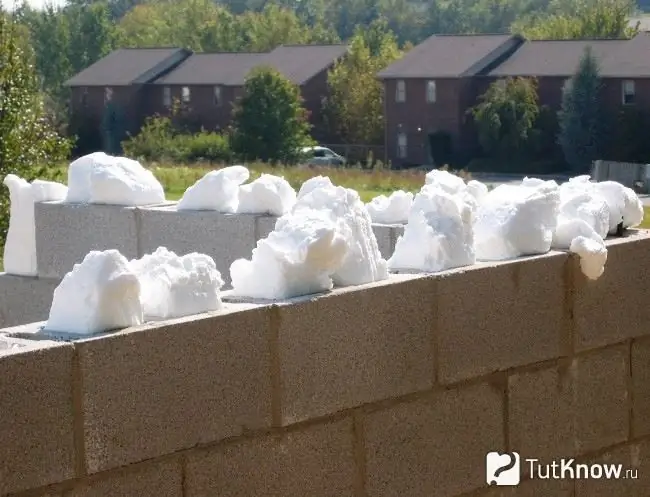
The undoubted advantages of liquid foam made this method of insulating houses, industrial buildings and outbuildings attractive and popular:
- The fine-celled, excellent steam-conducting texture of the foam actively passes through its entire volume of moisture from the walls to the outside, making them dry and counteracting the accumulation of condensate and the development of the accompanying fungal mold. This property makes the material "breathable", and this is of particular value for any, and especially wooden, walls.
- The fire safety of the jellied foam is quite high and has a combustibility not lower than the G-2 group. The material does not support combustion, and given the organic composition of the insulation, this phenomenon can be considered unique. In an open flame, the hardened foam is charred and loses its bulk, evaporating, without forming molten droplets, soot and poisonous gases.
- Penoizol tolerates changes in air humidity and temperature perfectly, without changing its internal structure and at the same time having a rare durability. Studies have determined the service life of this insulation at the level of 60-80 years.
- Like all heaters, jellied foam has excellent soundproofing properties. A layer of Penoizol 5-7 cm thick reduces mid-frequency airborne noise by 3 times, and structural noise by 2 times.
- The cost of liquid foam is low and affordable. Using this material, you can save at the stage of building a house, but more significant savings can be obtained on heating during its operation, since this insulation has better thermal insulation characteristics.
- A significant advantage of liquid thermal insulation is the absence of the need for careful surface preparation. This circumstance significantly reduces construction costs. If a special machine is used at the site for the manufacture of Penoizol, it will be sufficient to provide only access to electricity and water for its operation.
Like any other thermal insulation, wall insulation with liquid foam has its drawbacks:
- Compared to extruded foam, Penoizol has a low mechanical strength.
- If water gets on the insulation for a long time, it is able to absorb some of it, which worsens the thermal insulation properties of the coating. However, Penoizol can quickly evaporate the accumulated moisture due to its capillary structure.
- During the polymerization process, liquid foam emits a small amount of formaldehyde and water vapor into the air, but after the end of this process and getting rid of moisture within 2-3 weeks, the indicator of the presence of harmful substances does not exceed their maximum permissible concentration.
- In the case of injection of liquid insulation not into capital concrete or brick walls, but into frame walls, due to the problem of creating significant pressure in such structures, the filled foam has an unpleasant property - insulation shrinkage during its polymerization and drying, amounting to up to 1%.
Many of these shortcomings can be remedied. Thermal insulation made of liquid foam is protected by cladding from climatic factors and mechanical damage. In the frame walls, it is reinforced, this eliminates the shrinkage of Penoizol for the entire period of its operation, and also makes it possible to obtain a monolithic coating reinforced with fibers throughout the volume.
Wall insulation technology with liquid foam
Many slab insulation are made by polymerizing foamed raw materials. But if it is applied directly to the structure, the adhesion of the base and the material will be many times stronger. For this reason, mobile liquid foam stations have become very popular lately. With their help, the foam insulator is prepared at the site of its use. Let us consider in detail this technology of insulation with liquid foam.
Selection of material for wall insulation
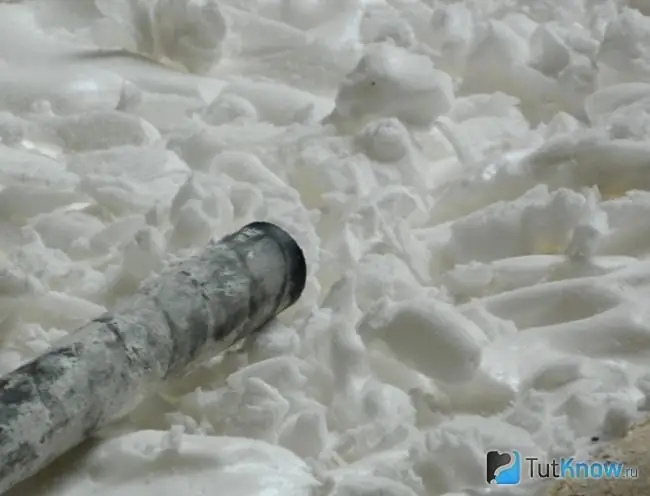
Pouring foam is made by foaming with compressed air a mixture consisting of urea resin, an acid curing catalyst, a foaming agent and water. To increase the thermal insulation properties of the future coating and improve its technical characteristics, various modifiers can be added to the composition in an amount of up to 5% by weight of the resin.
The ingredients of the mixture are mixed and whipped until foam is obtained in a special installation. Air is supplied to it by a compressor with a capacity of at least 300 l / min.
The apparatus for the production of foamed insulation can be rented or purchased. Its cost ranges from 20,000 rubles and above. Expensive installations are controlled by microprocessors, which greatly simplifies the process of insulating structures.
If the scope of work on thermal insulation is small, you can use special cylinders filled with liquid foam, which are also commercially available. Shake the can vigorously 15-20 times before use. This is necessary so that the propellant is evenly distributed in its contents - an inert substance that provides excess pressure to displace the active composition.
In addition, when working with liquid foam in cylinders, you need to monitor the temperature regime of the mixture. Its temperature of + 20 ° C is optimal for application. If it is lower, the cylinder should be preheated in warm water, the temperature of which should not be higher than + 50 ° C. In summer, it is recommended to cool highly heated cylinders to the desired state.
Features of the calculation of liquid foam
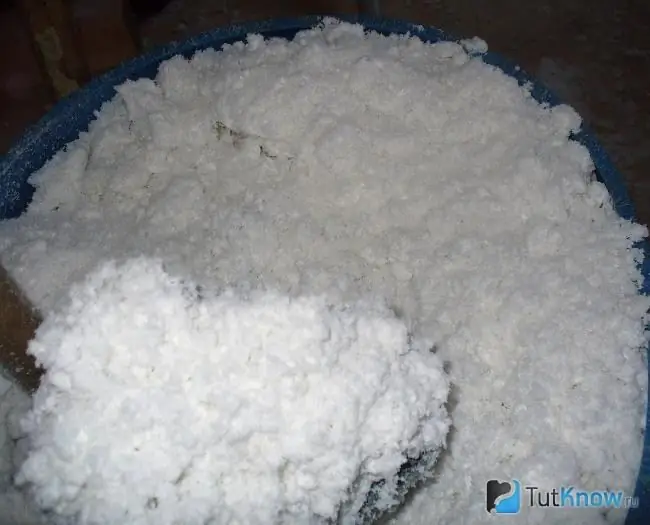
The calculation of the material should be done in cubic meters. The formula for it, taking into account a stock of 10%, looks like this:
V (volume) = wall length * wall height * thickness of the insulation layer (i.e. the cavity between the walls, which must be filled with liquid insulation).
Example 1
… It is required to pour foam plastic t. 10 cm into a wall measuring 10x4 m. Calculation of the volume of material: V = 10 * 4 * 0, 1 = 4 m3.
Example 2
… It is necessary to insulate the walls of the whole house with a size of 8x10 m and a height of 4 m. The thickness of the insulating layer should be 10 cm. In this case, to calculate the consumption of liquid foam, it is necessary to take into account 10% of the area of door and window openings. The total volume of material, taking into account all openings, will be: V = (8 + 8 + 10 + 10) * 4 * 0, 1 = 14, 4 m3… Excluding openings: V = 14.4 * 0.9 = 12.96 m3.
The cost of the required material can also be calculated, taking into account its average price of 70-80 rubles / m2.
Instructions for pouring liquid foam
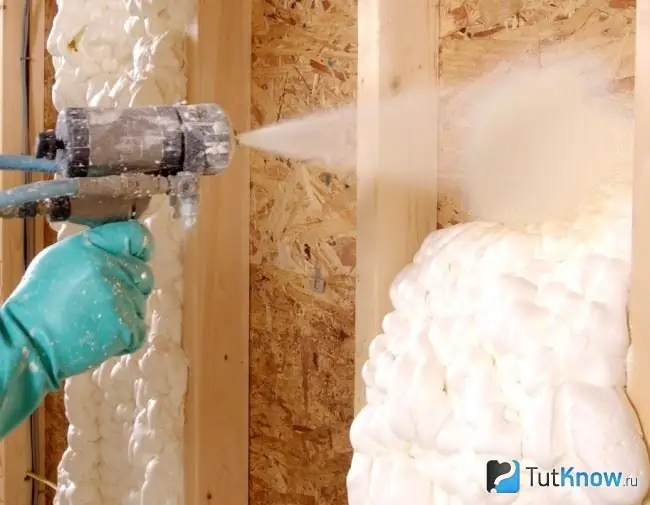
This procedure is distinguished, among other methods of insulation, by the absence of the need for surface preparation. After preparing the foaming mixture in the apparatus, filling the cavity between the outer and inner walls with liquid foam is carried out using a special hose with a diameter of 30 mm. The insulation is quite dense and of high quality.
This technology provides three options for its use:
- Pouring into the cavity between the walls of the building in use. This procedure can be performed if the free space is 3-5 cm in size. In a staggered manner with a step of 1 m, holes with a diameter of 32 mm are made in the wall. Then foam plastic is poured into each hole under pressure through a hose until it appears in the hole next to it.
- Pouring into the cavity between the walls of the building being erected. In this case, the cavity is filled with a mixture of several layers.
- Pouring insulation between the wall and the false partition, which can be trimmed with profiled flooring, drywall sheets, plastic and others. This method of insulation with liquid foam is also relevant for frame houses.
All cavities are filled from the bottom to the top of the wall. Penoizol does not increase in volume and fills completely hard-to-reach places, cracks and open pores.
After 20 minutes, the poured mass begins to harden, gaining initial strength over the next 3-4 hours. Final polymerization and drying of the material should be carried out under natural conditions for two to five days. After 3-4 weeks, the insulation is completely stabilized.
How to insulate a house with liquid foam - watch the video:

Choosing liquid foam for home insulation, you can get one of the best heat insulators on the construction market due to the high performance, durability and affordable price of this material. Good luck!